Fasi costruttive vettore Stratosfera
02/08/2003
PROTOTIPO SPERIMENTALE VETTORE STRATOSFERA
Parte 1 - LE FASI DI COSTRUZIONE PASSO PER PASSO
La costruzione del prototipo per la valutazione dell'avionica, sistema telemetrico e soprattutto del rientro automatico guidato da GPS sta procendo nonostante il caldo africano di questi mesi, problema che riguarda soprattutto la laminazione dei materiali compositi (la resina indurisce troppo rapidamente).
La cellula e' stata completata e queste sono le varie fasi costruttive, descritte passo per passo per illustrare il metodo di lavorazione dei materiali compositi.
Per il prototipo di valutazione e' stata scelta una scala ridotta a 1:1.5.
Il peso totale e' stimato in 6400 grammi, completo di motore, propellente, sistema di rientro, avionica, telemetria ed accessori.
Il Centro di Gravita' e' posizionato a 156 cm dall'ogiva, mentre il CP calcolato dalla equazioni di Barrowman risulta a 191 cm.
In queste condizioni la stabilita' risulta eccessiva, ma sara' possibile migliorarla con una diverso posizionamento del carico utile.
Questo e' il progetto della cellula, completo di dimensioni:
.gif)
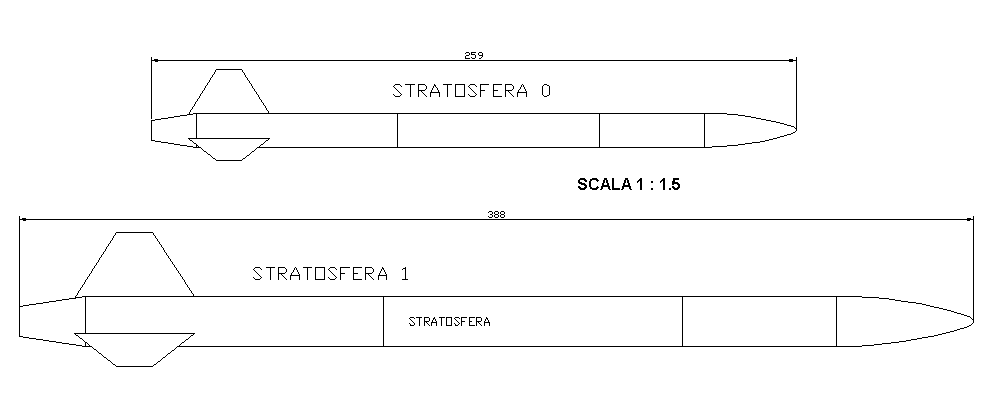
.jpg)
Parte 2 - COSTRUZIONE DEL CORPO PRINCIPALE
Come materiale per il corpo del vettore e' stata scelta la combinazione vetroresina/epoxy, precisamente un tessuto a grammatura leggera (80 gr/mq) a trama bidirezionale, largo 82 cm, avvolto in 10 strati sovrapposti.
Questo sistema garantisce una ottimale distribuzione delle sollecitazione lungo gli assi e una buona levigatezza superficiale.
Come metodo di laminazione e' stato usato quello a stampo positivo, che consiste nell'avvolgere il tessuto all'esterno del formatore cilindrico.
Per prima cosa e' stato necessario preparare il formatore per il corpo principale composto da una coppia di tubi in fibra di vetro con diametro esterno 135 mm e lunghi 810 mm.
Lo stampo e' stato ricavato da un tubo in PVC per impianti edili del diametro esterno di 125 mm.
Lo spessore richiesto per le pareti del tubo era di 1,2 mm, percio' il diametro del cilindro e' stato incrementato a 132,6 mm avvolgendo diversi fogli di carta patinata da 170 grammi/mq uno sopra l'altro.
Una volta raggiunto lo spessore desiderato, il tubo e' stato rivestito da tre strati di foglio di alluminio per uso alimentare (domopack), che hanno lo scopo di facilitare l'estrazione del manufatto dal formatore.
Questi fogli di alluminio hanno la caratteristica di non aderire l'uno sull'altro e percio' l'estrazione per scivolamento e' sicura e senza intoppi.
Sopra di questi e' stato posto un ulteriore rivestimento di pellicola trasparente avvolta a spirale sopra l'alluminio, che serve ad evitare l'infiltrazione di resina tra gli strati di alluminio e a facilitarne il distacco una volta terminata la laminazione.
Riassumendo, partendo dall'interno il formatore e' composto da :
Tubo in PVC, avvolgimento in carta a spessore, pellicola in alluminio, pellicola in polietilene.
Nell'immagine sottostante si puo' notare la composizione del sandwich:
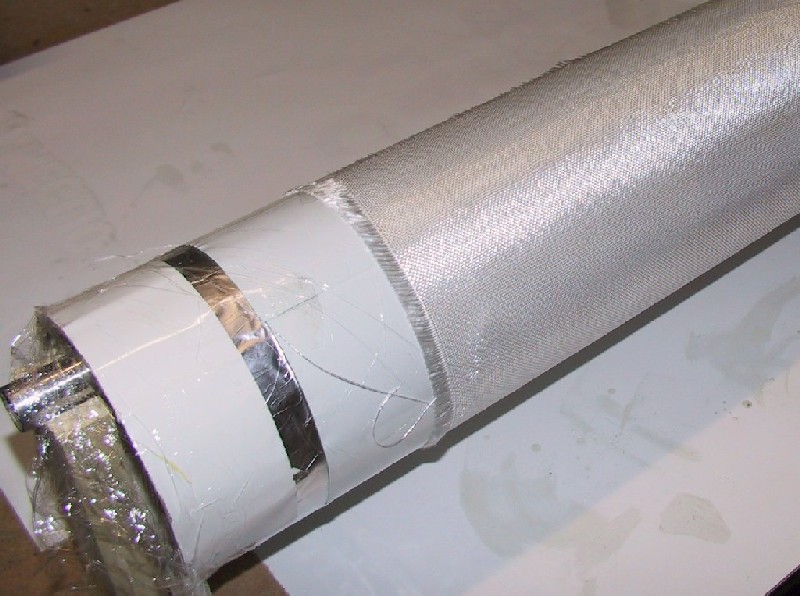
Particolare del tubo formatore
La resina epoxy e' stata preparata seguendo scrupolosamente il dosaggio prescritto dal produttore, nella fattispecie il rapporto era di 3 parti di resina e 1 di induritore.
Per questo scopo e' stata usata una bilancia digitale di precisione con risoluzione di 1 grammo.
Per la laminazione completa di un tronco cilindrico di 82 cm sono stati necessari 280 grammi di resina, suddivisi in 210 grammi di resina e 70 grammi di induritore.
Considerato che la temperatura ambiente era di 28 gradi e percio' evitare il rischio di polimerizzazione precoce, la resina e' stata preparata in 4 dosi da 70 grammi ciascuna, miscelate solo qualche minuto prima della laminazione.
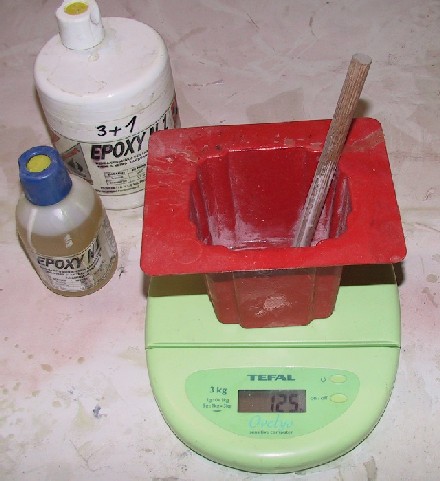
Preparazione della resina
Nel formatore e' stata infilata un'asta metallica appoggiata a due supporti laterali in legno alti 15 cm, in modo da sospendere il tubo senza fargli toccare il tavolo di lavoro lasciandolo pero' libero di ruotare.
Dopo aver fermato i lembi con del nastro adesivo il tessuto e' stato avvolto sul tubo per tutta la sua lunghezza, in questo caso poco piu' di 4 metri, tesandolo alla perfezione.
Solo dopo il tessuto e' stato impregnato di resina epossidica tamponandolo con un pezzo di gommapiuma, come si puo' vedere nella seguente foto. In questa fase e' d'obbligo l'uso dei guanti di lattice.
E' importantissimo che la resina penetri fino all'interno del rotolo, impregnando anche il primo strato del tessuto.
Per verificare questo basta osservare il suo colore: se e' bianco e opaco significa che ci sono delle inclusioni di aria, se e' di un colore omogeneo giallo chiaro e traslucido vuol dire che la laminazione e' buona.
L'aria presente nel tessuto deve assolutamente essere rimossa, pena un risultato insoddisfacente con la conseguente perdita del lavoro e del materiale.
Con la spugnetta di gommapiuma picchettiamo su tutto il tessuto in modo da infiltrare la resina dentro il tessuto e contemporaneamente spingere all'esterno le bolle d'aria.
Per questa operazione ci si puo' avvalere anche di un apposito rullo in metallo con delle scanalature superficiali.
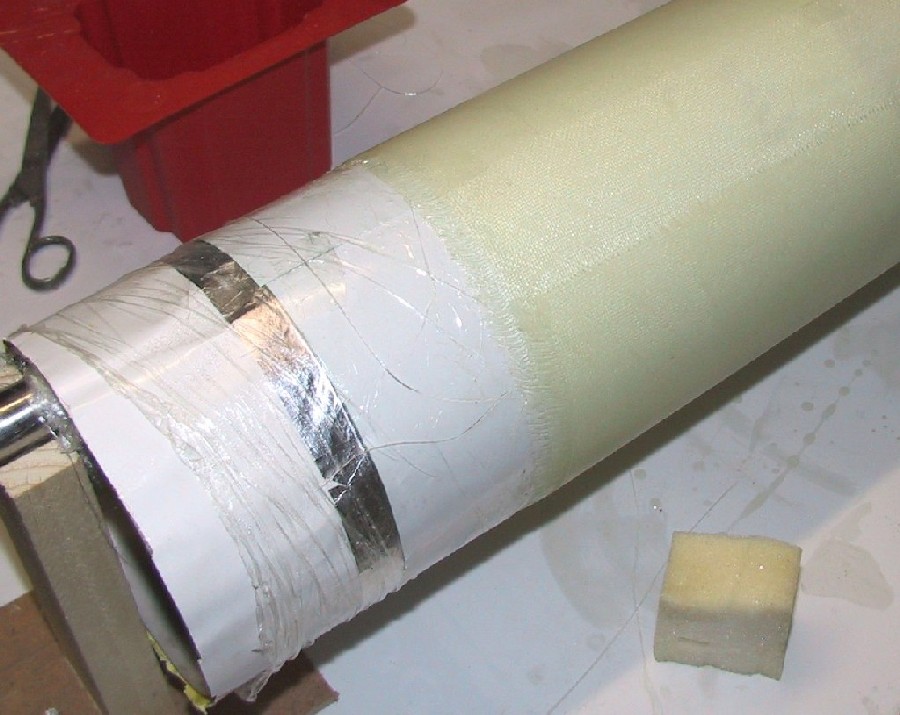
La fase di laminazione
Una volta che la catalizzazione e' terminata (almeno 10 ore di indurimento), possiamo sfilare il formatore dal tubo di vetroresina cosi' realizzato, la pellicola di alluminio permettera' allo stampo di scivolare fuori senza sforzo.
Possiamo ora togliere la pellicola di polietilene che riveste internamente il tubo.
Verra' via tutta intera e facilmente perche' la resina epoxy non aderisce al polietilene.
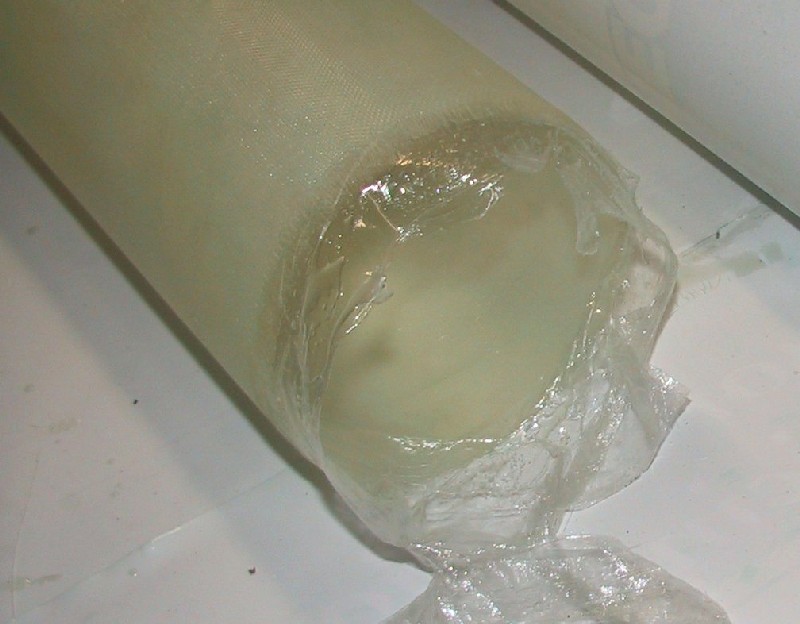
Il tubo estratto dal formatore
Ora possiamo tracciare il riferimento per il taglio dell'estremita'.
Per semplificare l'operazione possiamo avvolgere un foglio di cartoncino sul tubo, facendo coincidere i lembi e fissandoli con del nastro adesivo, poi con un pennarello tracciamo una linea seguendo il bordo in rilievo.
Con un seghetto per metallo tagliamo la parte in eccesso secondo la traccia, rendendo l'estremita' il piu' possibile piana e regolare.
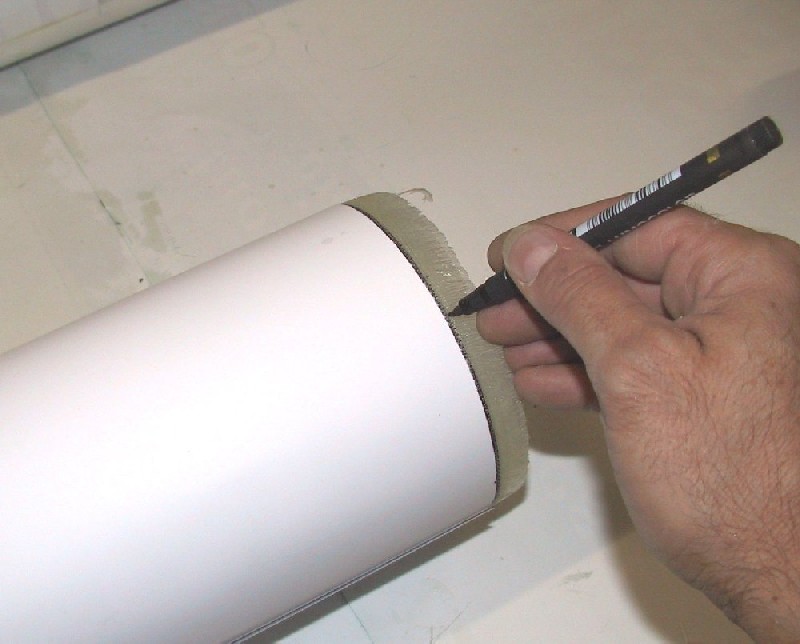
Tracciatura del bordo
Disponiamo cosi' di un tubo in vetroresina dall'aspetto abbastanza levigato, che rifiniremo ancora prima con carta abrasiva di grana 120 e poi ancora con quella piu' fine di grana 180.
Per il momento i pezzi rimarrano grezzi, la stuccatura fine la faremo al termine del lavoro.

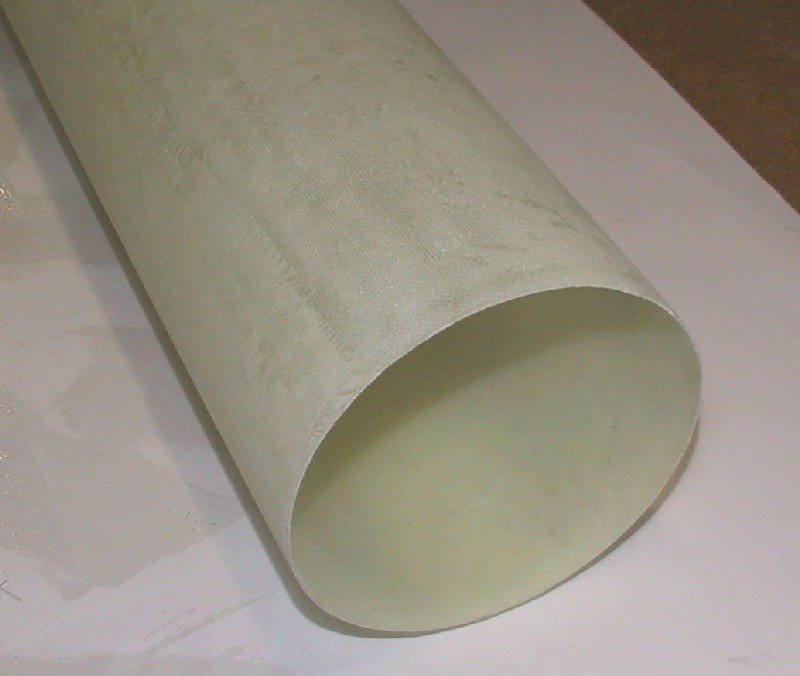
Il tubo prima e dopo la levigatura
Parte 3 - COSTRUZIONE DEGLI STABILIZZATORI AERODINAMICI
Con la medesima tecnica dobbiamo costruire un tubo di vetroresina con diametro interno 50 mm per accogliere il motore ibrido, il cono di coda secondo le misure specificate nel progetto e le pinne stabilizzatrici aerodinamiche.
Queste sono state realizzate con una lastra di compensato spessore 3 mm e rivestite dal tessuto in carbonio e kevlar GK210.
Le estremita' sono rastremate in modo da migliorare l'aerodinamica e per facilitare l'adesione del margini del tessuto.
Dopo aver ritagliato e sagomato il compensato, questo viene laminato con il tessuto e resina, poi viene infilato in un sacco un PCV e viene praticato il vuoto al suo interno. In questo modo la pressione atmosferica preme omogeneamente sulle superfici e si ottiene un risultato perfetto.
In mancanza di una pompa a vuoto si possono ottenere risultati accettabili anche inserendo il sacco tra due fogli di gommapiuma pressati con dei pesi.
A catalizzazione avvenuta il sacco puo' essere aperto, i bordi delle pinne devono essere ritagliati con un seghetto e levigati con carta abrasiva.
.jpg)
.jpg)
Costruzione del cono di coda
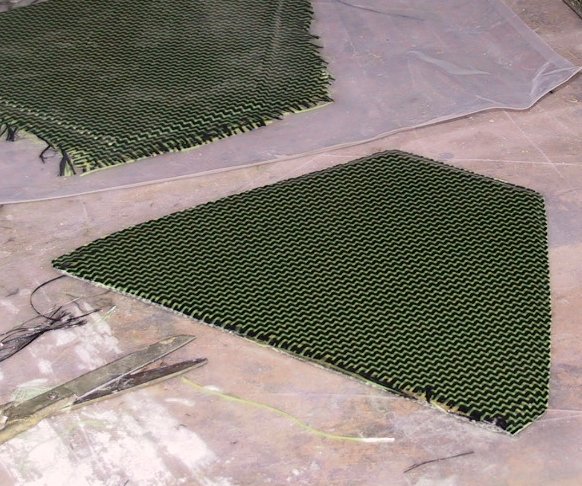
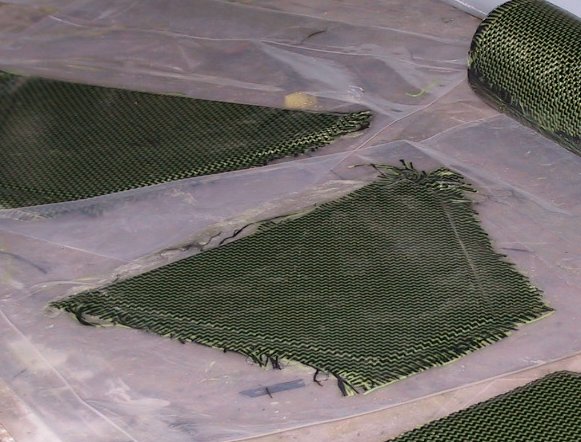
Costruzione delle pinne stabilizzatrici
Ora che disponiamo dei componenti necessari possiamo assemblare gli stabilizzatori.
Da un foglio di compensato da 5 mm ricaviamo dei settori circolari da 120 gradi che serviranno alla centratura deegli stabilizzatori.
Con dell'adesivo cianoacrilico denso li fissiamo provvisoriamente nella loro posizione ed infine laminiamo con tessuto GK210 per fissarli stabilmente.
Nel tubo del corpo principale ritagliamo tre fessure dello stesso spessore delle pinne.
Inseriamo il tubo nella struttura preparata in precedenza ed incollamo alla perfezione con colla epoxy oppure resina da laminazione.
Infine inseriamo il cono di coda e incolliamo anche quello.
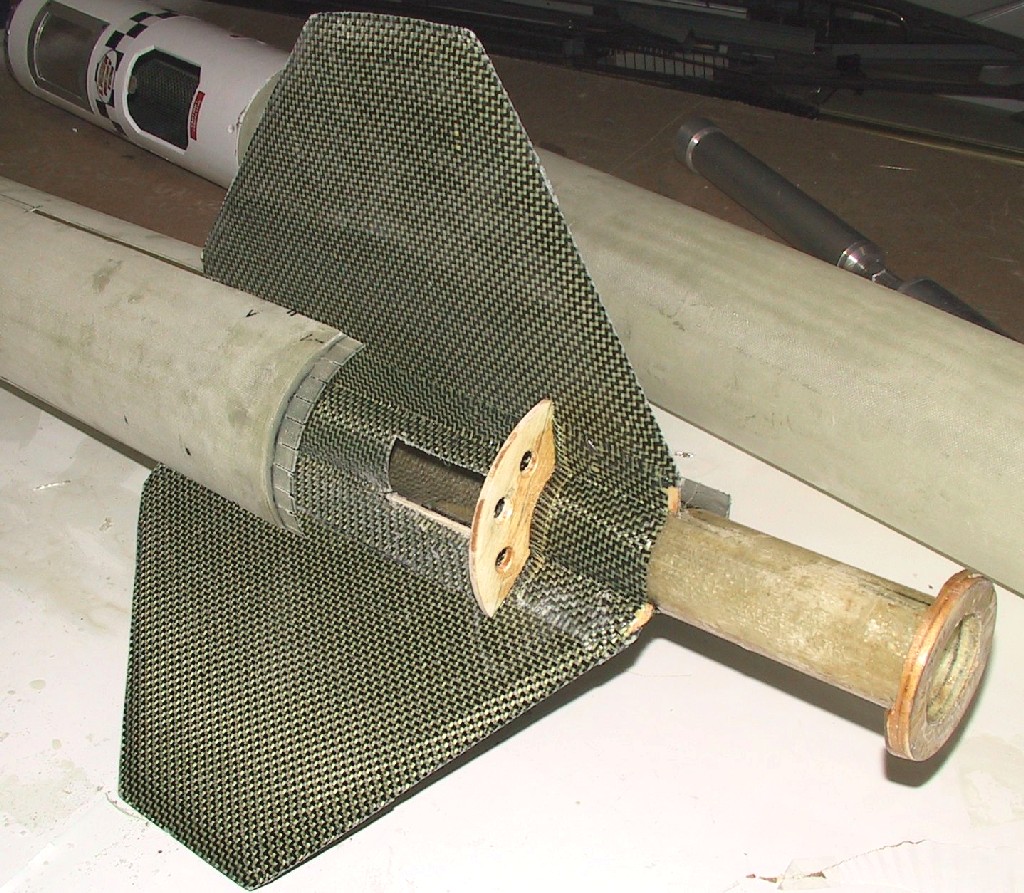
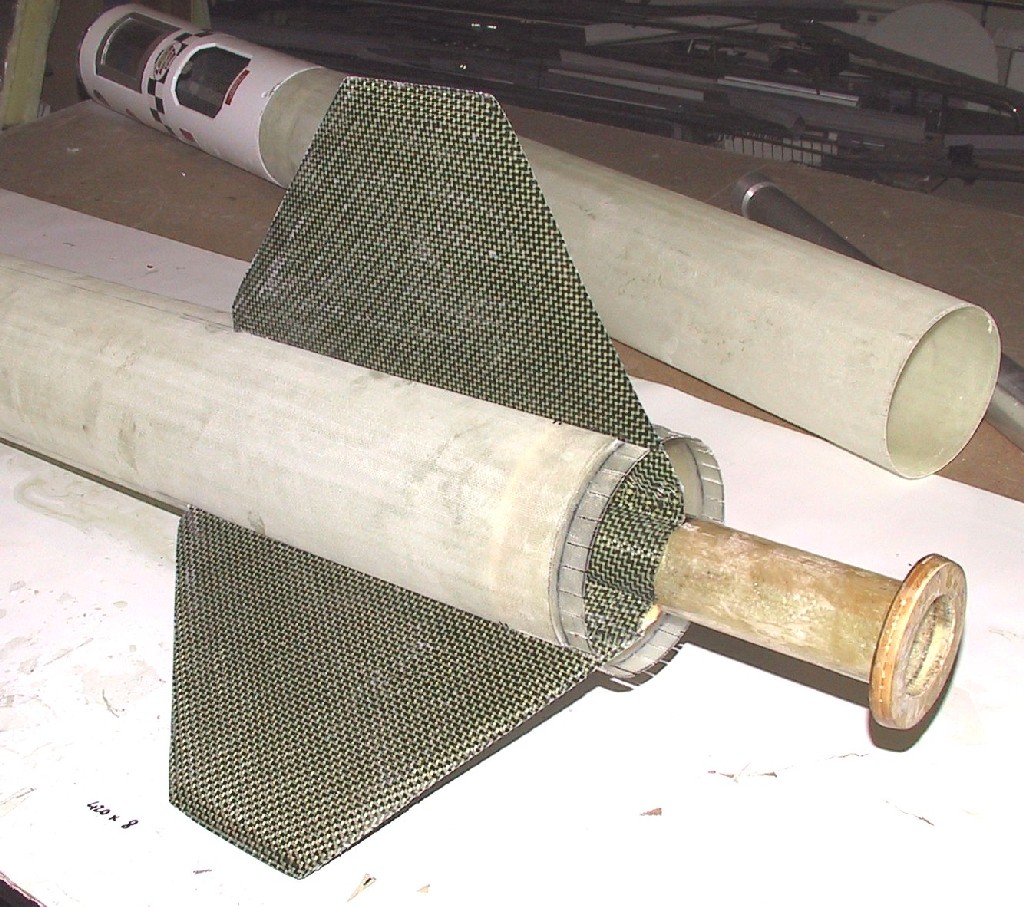
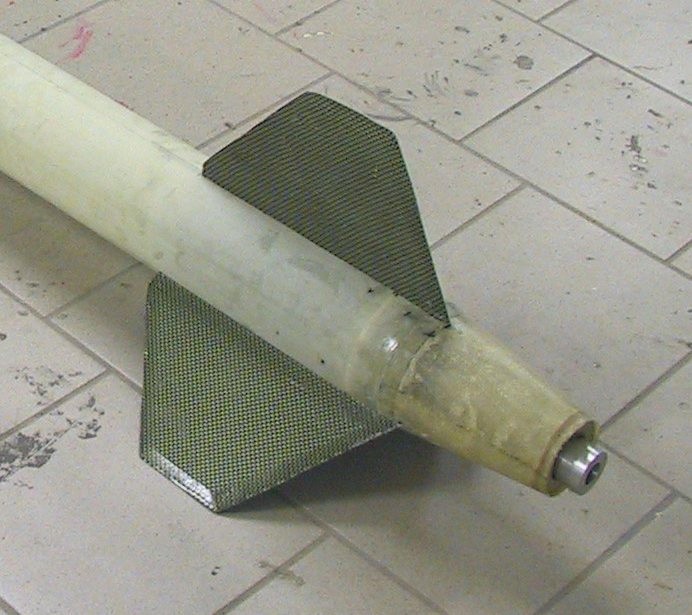
Assemblaggio delle pinne e del cono di coda
Parte 4 - COSTRUZIONE DELL'OGIVA
L'ogiva e' stata costruita con la procedura gia' descritta, solo che invece di un tubo cilindrico e' stato usato uno stampo positivo appositamente sagomato con un profilo parabolico.
Il formatore e' stato ricavato da un blocco di polistirene espanso ad alta densita', usato normalmente nel settore edile per isolamenti e sottopavimenti.
E' simile al polistirolo espanso ma non si sbriciola nelle famigerate palline che rendono difficile la lavorazione. Lo si trova in lastre di vari spessori, generalmente di dimensioni 60 x 120 cm.
L'ogiva in questione richiedeva uno spessore notevole, percio' sono stati incollati con epoxy tre lastre che poi sono state sbozzate con la sega a nastro.
Il blocco cosi' ricavato e' stato poi sottoposto a tornitura per mezzo di un trapano dotato di uno speciale accessorio.
Dopo la rifinitura con carta abrasiva media e fine l'ogiva e' stata laminata con la solita resina e tessuto in fibra di vetro.
La parte terminale, essendo arrotondata ha richiesto una accurata disposizione del tessuto, tagliato a settori triangolari ed applicato in strati sovrapposti.
Queste sono le fasi di lavorazione e il risultato finale.

Sbozzatura dell'ogiva
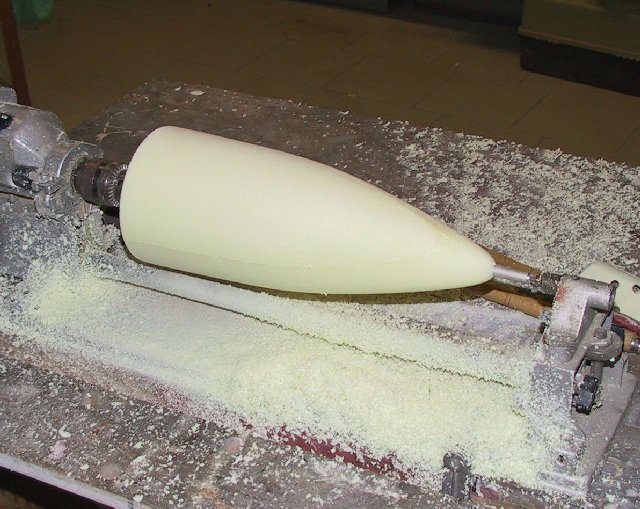
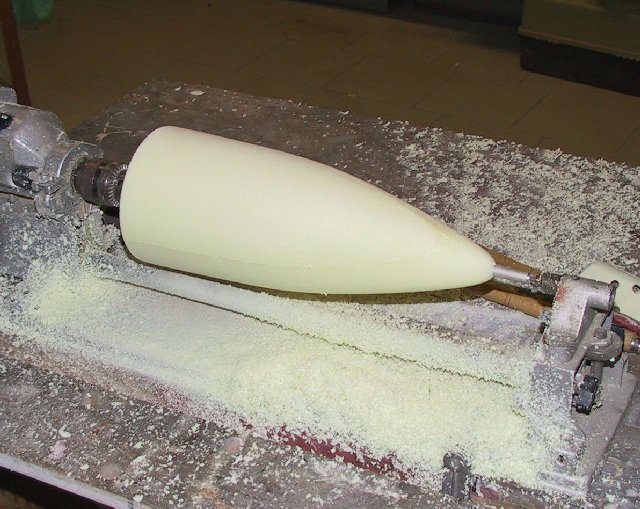
Tornitura e rifinitura
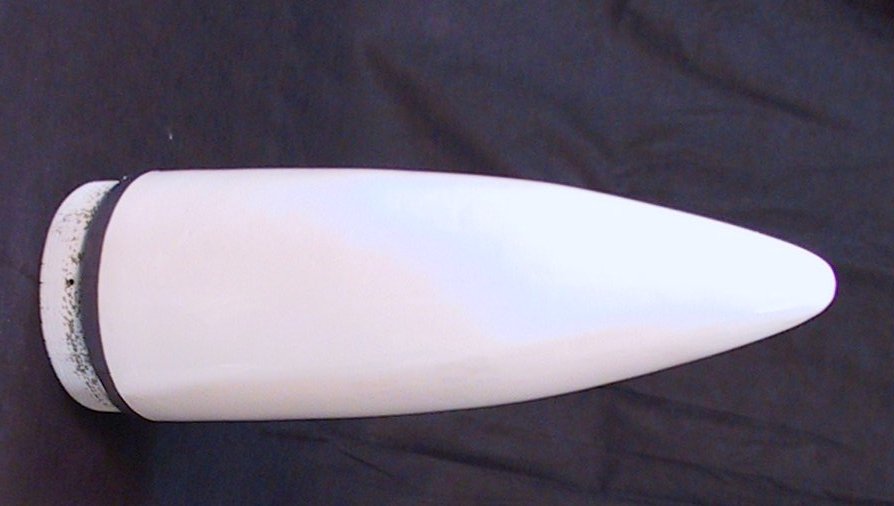
Il risultato finale dopo la laminazione
Parte 5 - COSTRUZIONE DELLA CAPSULA PAYLOAD
La costruzione della capsula payload, per la necessita' di ottenere una struttura particolarmente robusta a protezione della strumentazione elettronica, ha richiesto una tecnologia piu' complessa.
E' stata scelta una configurazione a sandwich, con uno strato in fibra di carbonio e kevlar per la parte interna ed uno strato di fibra di vetro per la parte esterna.
Nel mezzo e' stato inserito uno strato di TERMANTO, uno speciale materiale espanso a base di poliuretano, pretagliato per permetterne la sagomatura.
La fibra di carbonio e kevlar utilizzata e' la GK210 da 210 grammi/mq distribuita dalla ditta Angeloni di Mestre.
Il metodo di lavorazione e' molto simile a quello gia' illustrato :
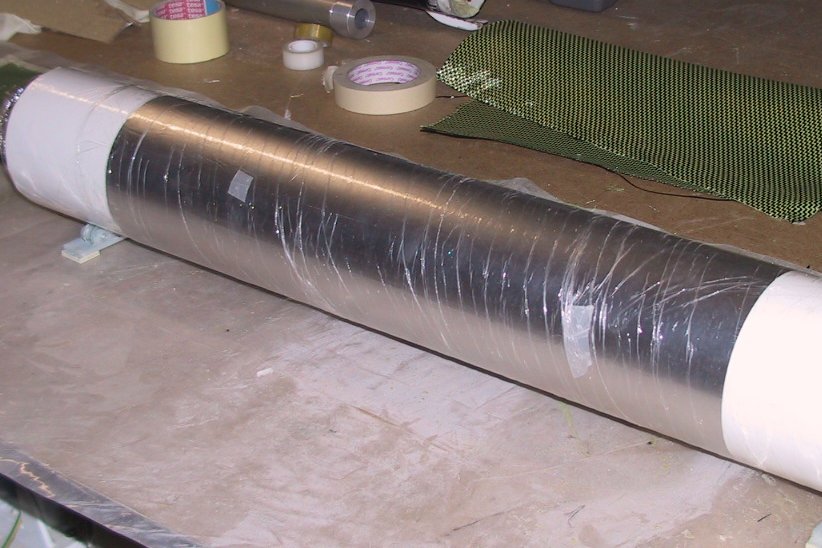
Preparazione del formatore con foglio di alluminio e polietilene
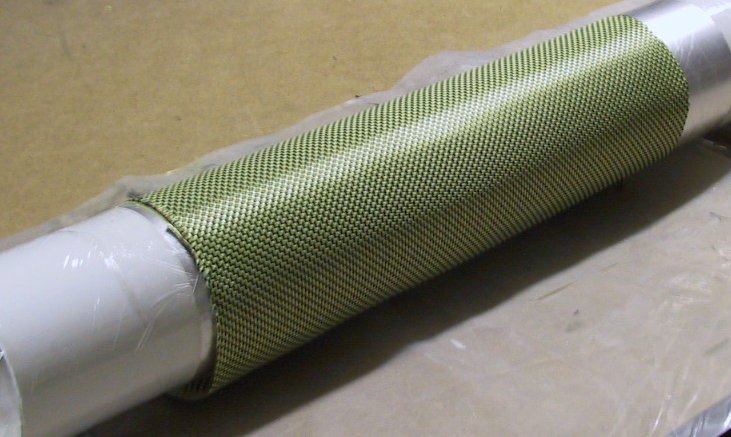
Laminazione del tessuto in carbonio/kevlar
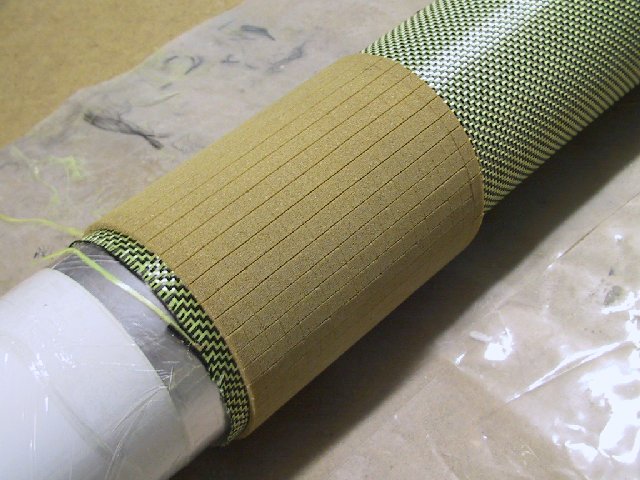
Stesura del termanto
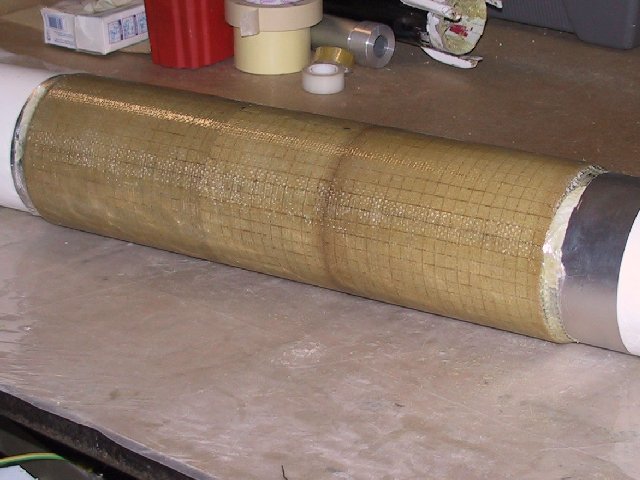
Laminazione dello strato esterno in fiberglass
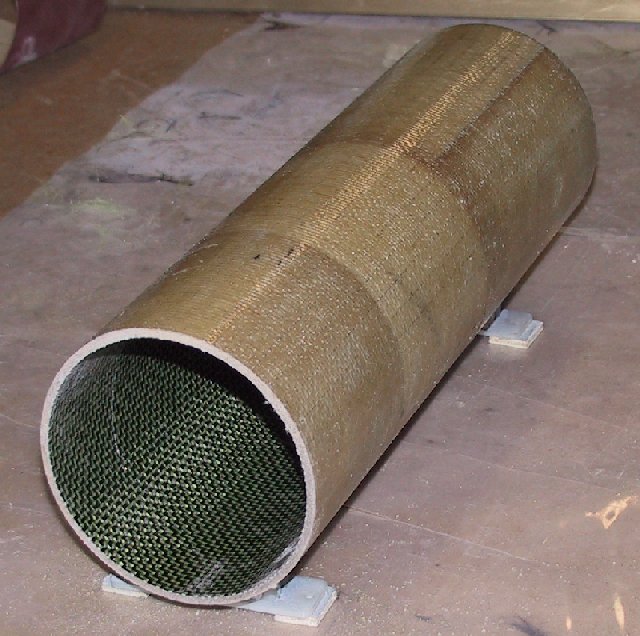
Pronto per la rifinitura
Parte 6 - LA STUCCATURA E RIFINITURA
La rifinitura di tutti i componenti descritti e' stata eseguita con un particolare stucco, caratterizzato dall'estrema leggerezza.
E' preparato miscelando della resina epossidica con delle speciali cariche, in questo caso delle microsfere di vetro cavo (microballons).
Hanno l'aspetto di una polvere bianca finissima ed impalpabile e miscelandole con la resina si trasformano in una "pappa" giallastra dalla consistenza cremosa, percio' tixotropica (non cola).
La percentuale resina/microsfere e' variabile ma non e' critica, per stuccature che richiedono una certa resistenza meccanica si puo' miscelare una parte di resina e due di microsfere (misurate in volume).
Per stuccature leggere come quelle superficiali o riempitive si puo' aumentare il rapporto a 1 a 3 oppure 1 a 4.
Piu' e' alta la percentuale di microsfere piu' leggero e' lo stucco, ma le resistenza meccanica peggiora, occorre percio' trovare il giusto compromesso. Una volta polimerizzato, questo stucco e' facilmente carteggiabile e la superficie risulta molto levigata.
In certi punti, come ad esempio le attaccature delle superfici aerodinamiche, e' necessario abbondare con lo stucco per raccordare l'angolo vivo ed ottenere un eccellente effetto estetico.
Lo stucco va steso in modo regolare ed omogeneo su tutta la superficie in composito, in modo da ricoprire le cavita' tipiche del tessuto. Per questa operazione e' necessaria una spatola in materiale flessibile, ottima anche una carta di credito scaduta o un ritaglio di plastica.
Quando lo stucco e' indurito dev'essere accuratamente levigato con carta abrasiva di grana progressiva, iniziando dalla 100 per finire con la 280, quest'ultima usata possibilmente insieme all'acqua.
Dopo la stuccatura e levigatura e' necessario applicare una o piu' mani di "fondo". Si tratta di una vernice spray opaca, serve a creare uno spessore carteggiabile e a far aderire la verniciatura finale.
Per questa e' stata scelta una prima e seconda mano di smalto acrilico bianco opaco ed una terza mano di vernice trasparente a due componenti (ISOFAN). Si ottiene cosi' una superficie lucida e brillante, molto resistente ai graffi ed alle intemperie.
Per le colorazioni ci si puo' sbizzarrire a volonta', tenendo conto che i colori accesi permettono una maggiore visibilita' durante il lancio e i colori troppo scuri (nero o grigio antracite) tendono a far surriscaldare la cellula quando e' esposta al sole per lungo tempo.
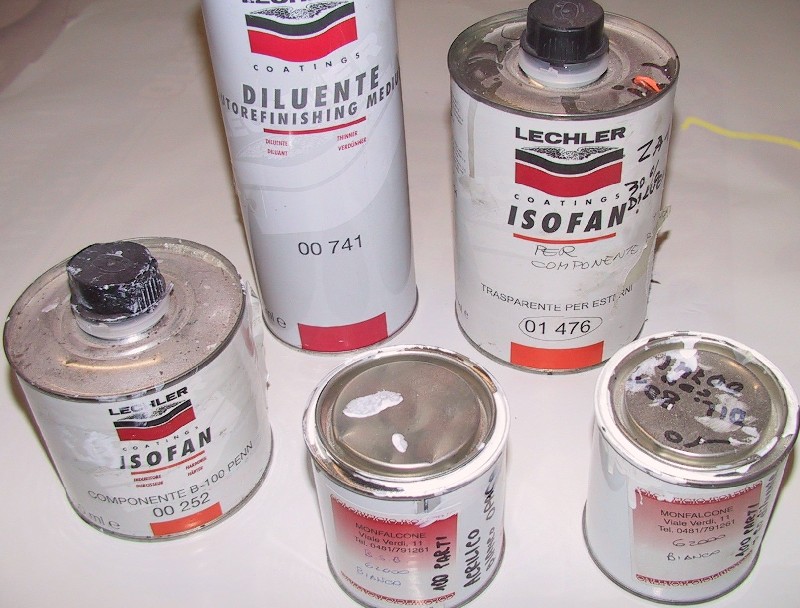
Smalti e vernici
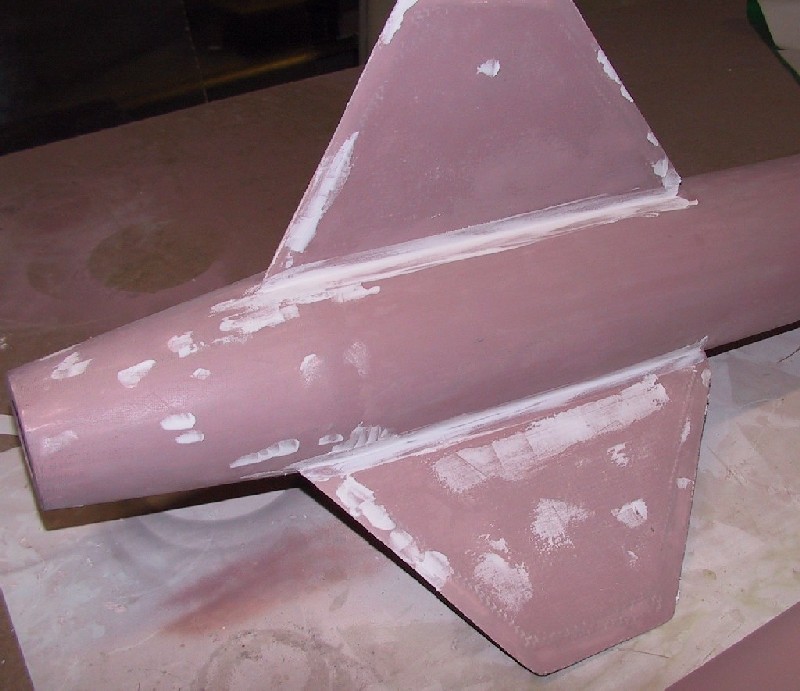
Stuccatura e rifinitura della cellula

Mano di fondo
Parte 7 - IL PORTELLONE PER L'ESPULSIONE DEL PARACADUTE
Il dispositivo di rientro guidato viene espulso da un portellone laterale ricavato sul corpo principale del vettore.
Questo sistema consente un'apertura "pulita" ed affidabile, senza l'impiego delle tradizionali cariche pirotecniche usate per pressurizzare l'interno della cellula, tristemente note per la loro scarsa affidabilita'. Inoltre in questo modo non e' necessaria la separazione fisica delle diverse sezioni del vettore che atterra integro in tutti i suoi componenti.
L'apertura del portellone, attivata da un servocomando aeromodellistico ed asservito da una apposita molla, permette l'uscita del paracadute pilota (drougue), che estrae la sacca contenente la vela alare ripiegata ed il blocco servomotore per il controllo del rientro guidato.
Il meccanismo di sgancio del portellone e' composto da due chiavistelli che lo bloccano in posizione di chiusura e che al momento richiesto liberano i ganci presenti sul portellone.
Le guide sono realizzate in tubetto di ottone da 3 mm mentre le aste di comando sono in ottone oppure acciaio armonico da 2mm.
Le estremita' scorrevoli sono sagomate a cono per facilitare la chiusura. Sul portellone mobile sono fissati i ganci, anch'essi costruiti con tubetto in ottone da 3 mm.
Il fissaggio e' stato eseguito saldando i tubetti ad una piastrina in ottone a sua volta incollata con adesivo epoxy alla parte mobile.
Nel seguente disegno si puo' vedere com'e' strutturato il dispositivo.
Disegno del dispositivo di sgancio
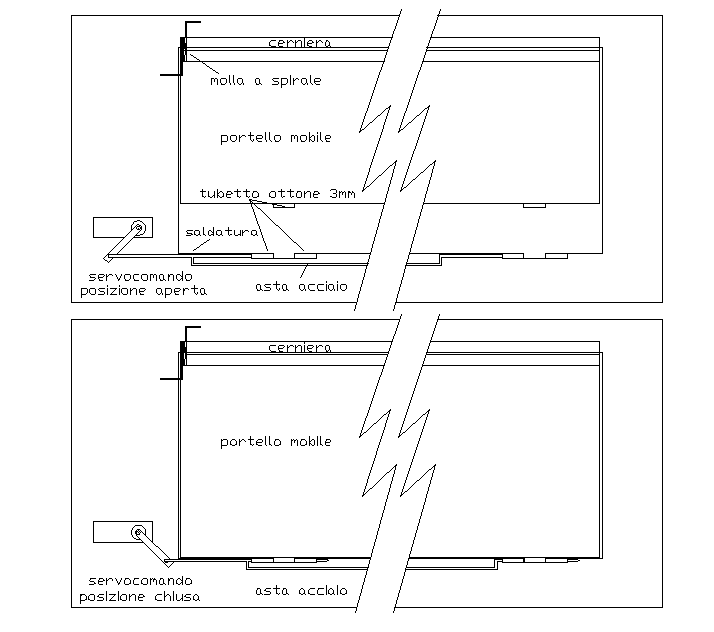
Schema del dispositivo di sgancio
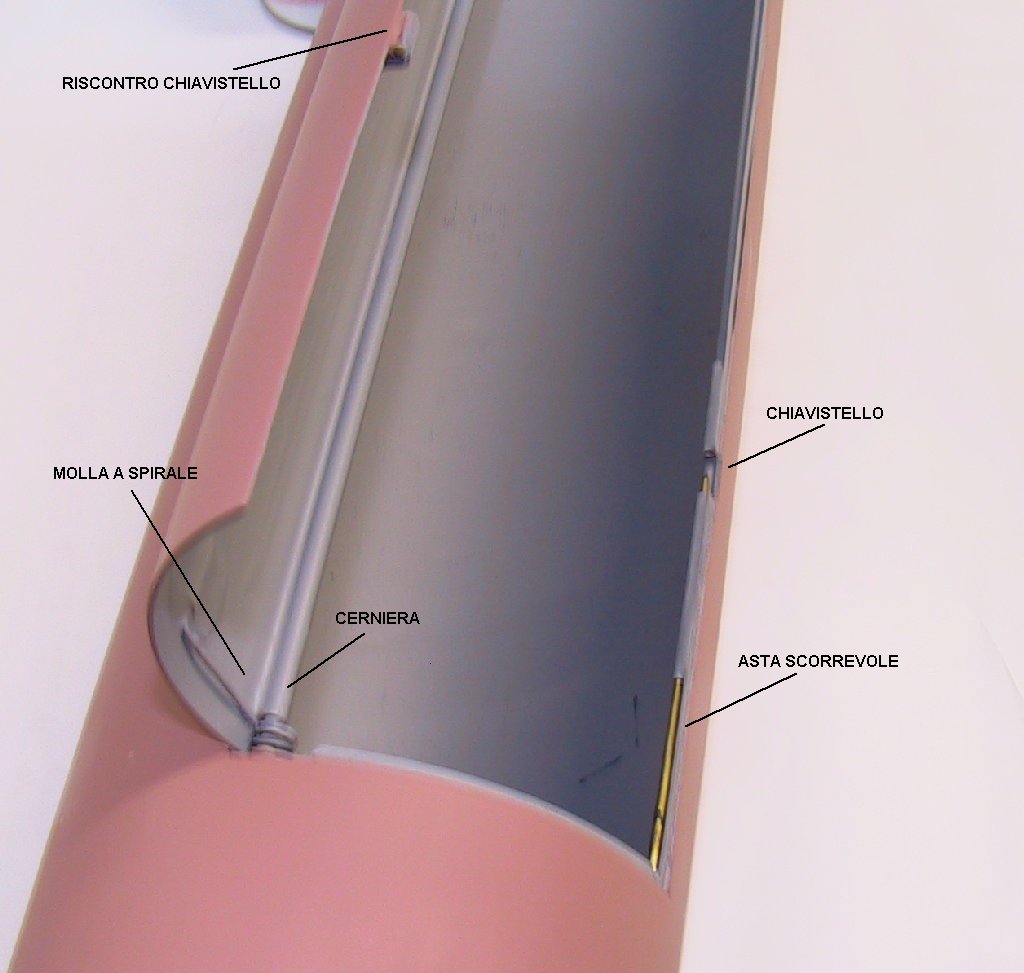
Particolare del dispositivo di sgancio
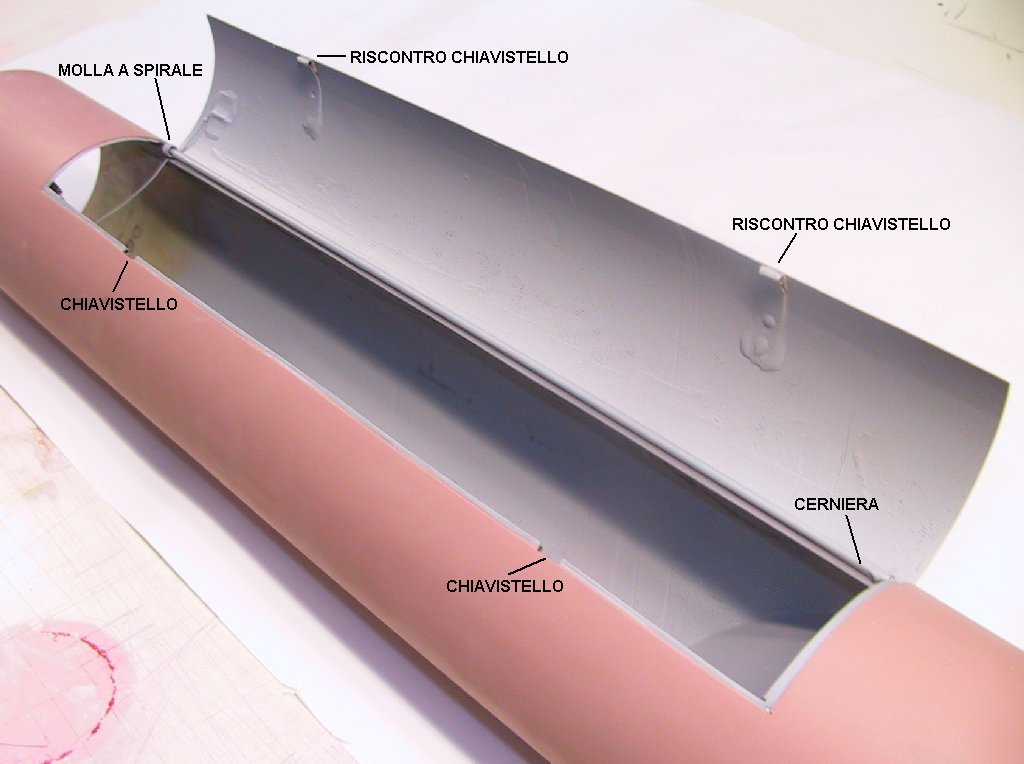
Particolare del portellone

Particolare del chiavistello
Parte 8 - I PORTELLI DI SERVIZIO
Sulla cellula sono stati ricavati il portellone per l'espulsione del paracadute di rientro e i due portelli di servizio per le manutenzioni dell'elettrovalvola del motore e il raccordo per il caricamento dell'ossidante.
Sono stati realizzati tagliando le pareti della cellula per mezzo di uno speciale utensile, una sorta di micro sega circolare che pero' vibra ad alta frequenza invece di ruotare. Si chiama "FEIN MULTIMASTER" ed e' anche in grado di levigare, sverniciare, eseguire incastri e mortase. I vantaggi sono un'eccellente precisione e un basso spessore di taglio.
Una volta praticati i tagli sono state montate le cerniere. Invece di impiegare normali cerniere metalliche (pesanti) o quelle miniaturizzate per aeromodellismo (troppo fragili) ho preferito realizzarle "ad hoc" per questa applicazione. Sono fatte con dei tubetti in fibra di carbonio dentro i quali e' infilata una barra in acciaio armonico di 2 mm di spessore.
I due tubi terminali, lunghi ciascuno 30 mm, sono incollati con epoxy all'interno della cellula, quello centrale, lungo quanto il portello, e' incollato sullo stesso, sempre con adesivo epoxy.
Essendo il cardine liberamente sfilabile, il portello e' smontabile secondo necessita'.
Il meccanismo di chiusura dei portelli di servizio e' molto semplice.
E' composto da una vite 3MA che attraversa lo spessore del portello, alcune rondelle, un dischetto metallico tagliato su un bordo e un dado 3MA. Il disegno sottostante spiega i dettagli costruttivi.
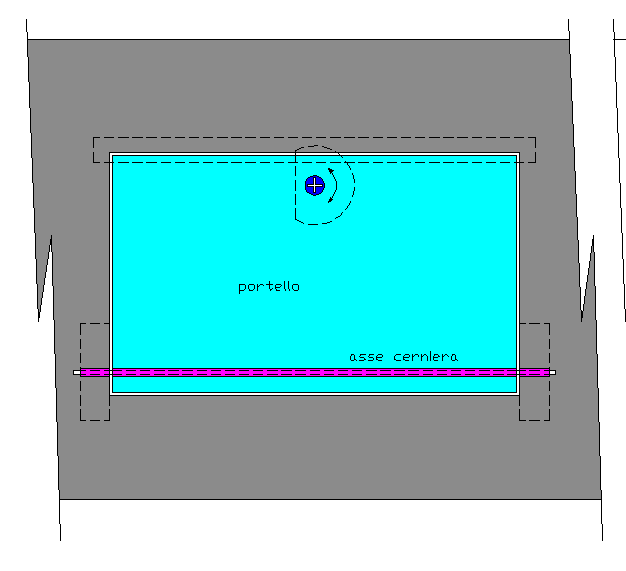
Disegno del meccanismo di chiusura BLOCCATO
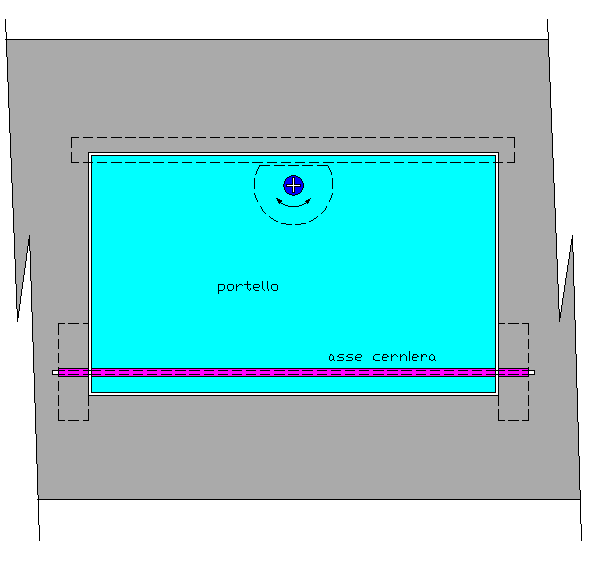
Disegno del meccanismo di chiusura SBLOCCATO
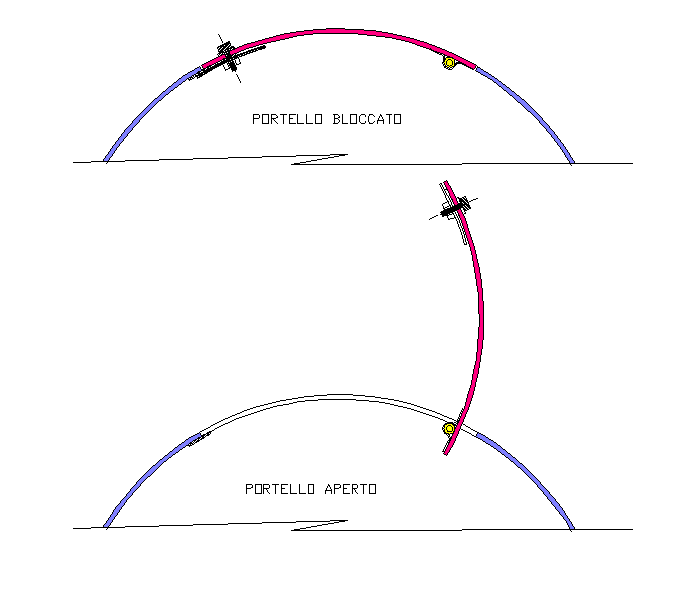
Sezione del meccanismo di chiusura
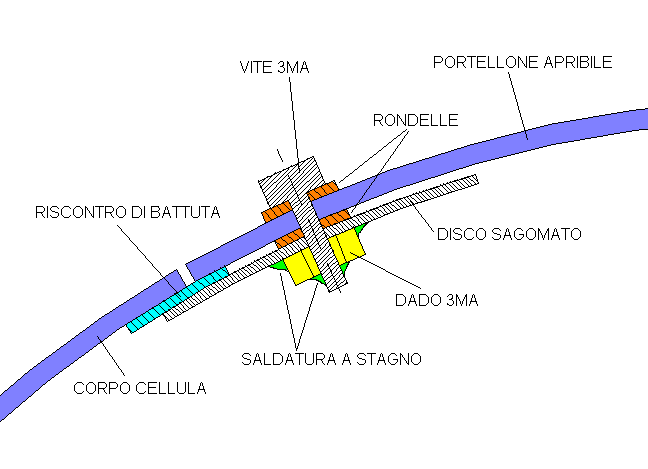
Particolare del meccanismo di chiusura
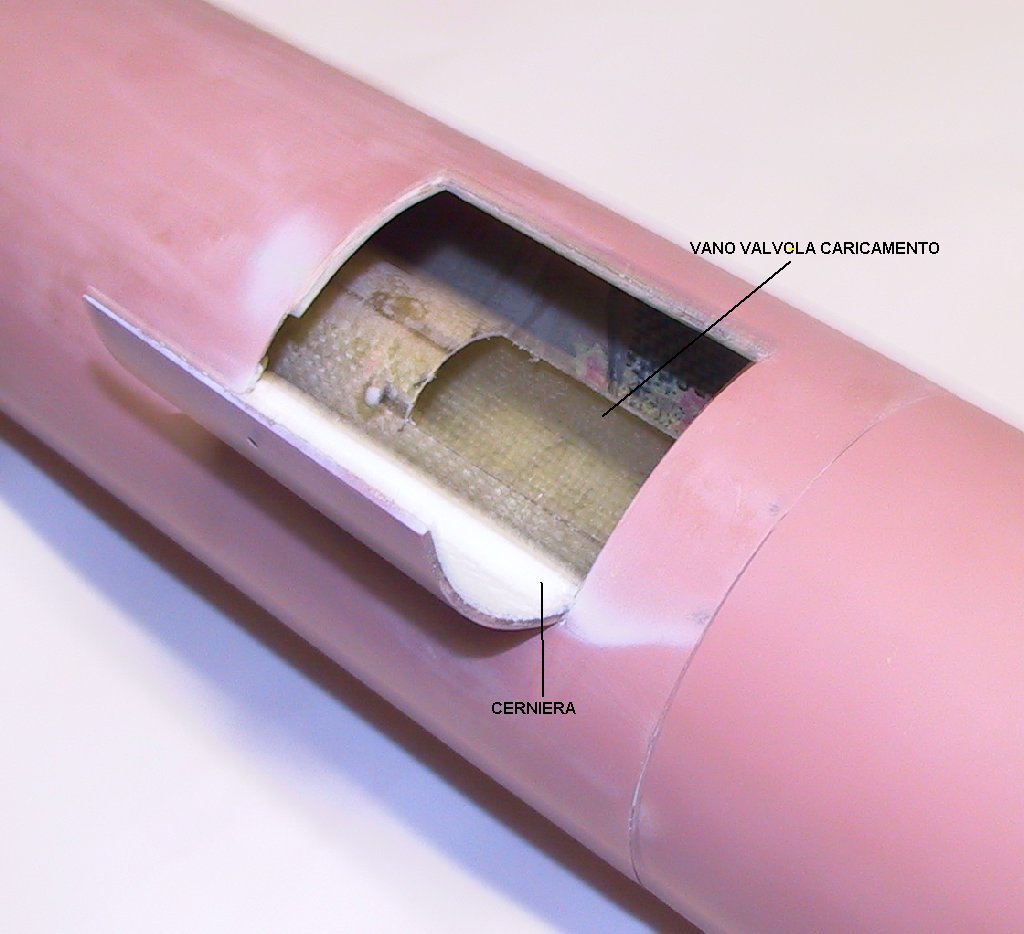
Particolare del portello centrale
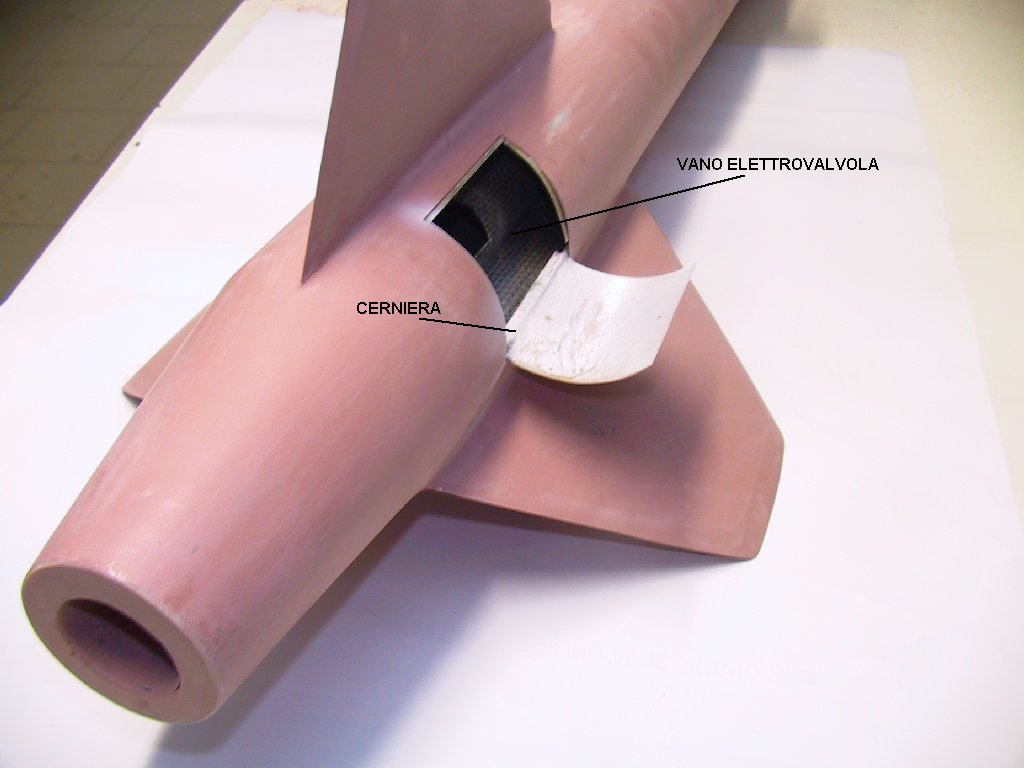
Particolare del portello inferiore
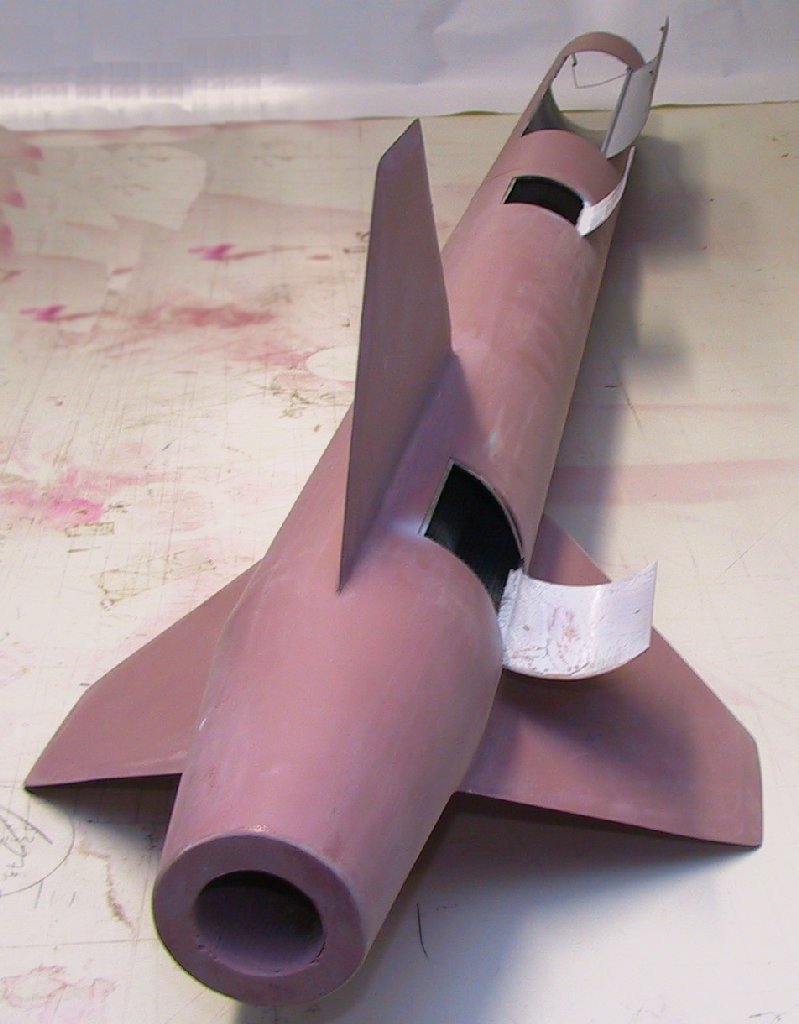
Vista d'insieme
Parte 9 - LA VERNICIATURA
La verniciatura e' una fase importantissima per la riuscita del lavoro. Da essa dipende l'aspetto finale dell'insieme e percio' e' fondamentale che sia eseguita in modo impeccabile e professionale.
Il tipo di smalto raccomandato per la finitura e' quello bicomponente applicato a spruzzo. In questo modo l'essicazione sara' molto veloce e la superficie risultera' lucida e brillante e soprattutto molto resistente ai graffi.
I tipi piu' adatti sono gli smalti a base epossidica o poliuretanican (Isofan o similari).
L'ambiente di lavoro dovra' essere pulito e senza polvere in sospensione.
Dovra' essere adeguatamente ventilato per evitare il ristagno di vapori ma allo stesso tempo non dovra' essere esposto ad eccessiva corrente d'aria.
E' fortemente raccomandato l'uso di adeguato abbigliamento da lavoro : una tuta in carta usa e getta e un berretto, degli occhiali, una mascherina filtrante (possibilmente al carbone attivo) e dei guanti in lattice.
Dopo aver levigato accuratamente tutti i componenti, questi vengono assemblati e sistemati in posizione verticale con il cono di coda verso l'alto.
Per la preparazione dello smalto si procede mescolando per alcuni minuti i due componenti nelle proporzioni indicate dai fabbricanti e poi vengono introdotti nel serbatoio dell'aerografo.
Una nota che merita una particolare attenzione :
Le pistole a spruzzo (o aerografi) necessitano di una precisa messa a punto per essere usate nelle migliori condizioni.
Generalmente le calibrazioni sono le seguenti (anche se dipendono dal modello di aerografo che si possiede) :
- Diluizione della pittura con la giusta quantita' di diluente (dipende dallo smalto usato, seguire le indicazioni del fabbricante).
- Regolazione del riduttore di pressione presente sul compressore, solitamente intorno a 4 bar.
- Regolazione del flusso di vernice (e' una manopola presente sulla parte sinistra dell'aerografo).
- Regolazione della corsa della valvola a spillo, controllata dal grilletto di spruzzo (e' presente di solito sulla parte posteriore dell'aerografo).
- Regolazione del deflettore di spruzzo che e' quella flangia girevole posta sulla parte anteriore dell'aerografo.
Se e' posto in posizione verticale lo spruzzo presentera' una forma ovale con l'asse verticale piu' lungo.
Se invece e' orizzontale il profilo di spruzzo avra' l'asse orizzontale piu' lungo. Tutto comunque dipende dalla forma dell'oggetto che dobbiamo verniciare.
La quantita' di vernice non deve essere eccessiva per evitare delle colature che rovinerebbero il lavoro. Si comincia con degli spruzzi di prova su un pezzo di legno o cartone con le valvole quasi del tutto chiuse, aprendole lentamente fino a trovare il punto giusto.
Una regolazione corretta si riconosce dalla leggera nebulizzazione prodotta dall'aerografo, che deve depositarsi quasi del tutto sull'oggetto da verniciare.
Se la quantita' di vernice e' eccessiva, una buona parte della nebulizzazione rimarra' sospesa in aria, appestando l'ambiente e depositandosi sul pavimento. Inoltre si formeranno immediatamente delle gocciolature.
Per la pitturazione di un pannello rettangolare la passate dovranno essere date prima in senso verticale (con il deflettore in posizione verticale), muovendo il polso a velocita' costante in entrambi e sensi di verniciatura, seguendo una immaginaria griglia a scacchiera.
Dopo alcuni minuti daremo delle passate in senso orizzontale con lo stesso metodo, avedo pero' l'accortezza di girare il deflettore in posizione orizzontale.
E' importantissimo non indugiare con lo spruzzo su un singolo punto (che apparentemente ci sembra bisognoso di pittura), ma e' necessario procedere omogeneamente su tutta la superficie.
Solo dopo che questo primo strato si sara' essicato potremo dare una seconda mano, correggendo eventualmente le mancanze della mano precedente.
L'ultima mano e' quella piu' importante e critica, non devono essere commessi errori altrimenti il lavoro sara' compromesso irrimediabilmente.
Per questa mano la pittura dovra' essere leggermente piu' diluita delle mani precedenti, in modo da ottenere un'aspetto lucido e brillante.
Al termine del lavoro ricordarsi di pultire perfettamente l'aerografo smontandolo nei suoi suoi principali componentie lavandoli accuratamente nel diluente indicato per il tipo di pittura impiegata.
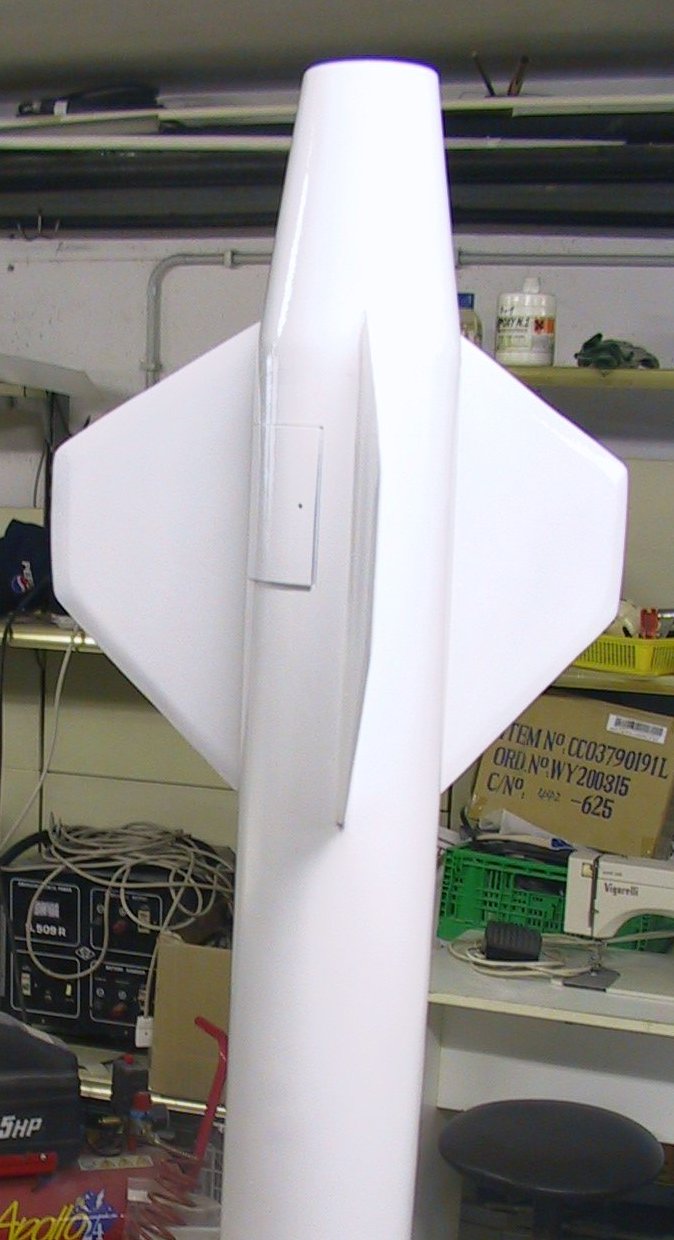
Verniciatura in corso
Parte 10 - LA VELA ALARE
Una caratteristica abbastanza innovativa del progetto Stratosfera consiste nel dotare il suo sistema di rientro con un dispositivo di guida automatica avente lo scopo di far atterrare il vettore nei pressi della zona di lancio.
Un ricevitore GPS rileva la posizione in cui si trova al momento dell'apogeo e la confronta con quella memorizzata al momento del lancio.
Per far questo e' indispensabile adottare un paracadute in grado di dirigere la discesa secondo una determinata rotta, percio' il classico paracadute a cupola non si presta a questo scopo, essendo per sua natura "non direzionale".
E' cosi' stata scelta una speciale configurazione conosciuta come "vela alare".
Consiste in un paracadute con sezione simile ad una centina di aereo, pur non essendo una struttura rigida.
Il profilo e' generato dell'aria presente nei "cassoni alari", spinta dalla sola pressione aerodinamica creata dall'avanzamento.
Questa configurazione, invece di creare una semplice resistenza alla discesa, e' in grado di generare un portanza e percio' un vero e proprio veleggiamento su lunga distanza, esattamente come un aliante.
Il sostentamento e' dato dal profilo curvo della superficie superiore della vela e precisamente per la differenza di velocita' tra lo stato laminare inferiore e superiore.
Ad ogni metro percorso sull'asse verticale (discesa) della vela, corrisponde un determinato avanzamento sull'asse orizzontale.
Il rapporto tra questi due valori indica l'"efficenza" della vela alare.
La caratteristica piu' interessante di questo tipo di paracadute e' pero' quella di poter dirigere la discesa seguendo una certa rotta semplicemente modificando l'inclinazione dei bordi d'uscita della superficie aerodinamica.
Per ottenere questo effetto e' sufficiente applicare dei cavetti sulla sezione posteriore dell'ala e tirarli secondo necessita'.
Trazionando il tirante destro la vela virera' a destra e viceversa.
Naturalmente questa operazione dovra' essere eseguita per mezzo di un servomotore e di un meccanismo avvolgitore che tirera' i cavetti secondo le indicazioni fornite dal sistema di guida computerizzato.
.jpg)
La vela alare aperta
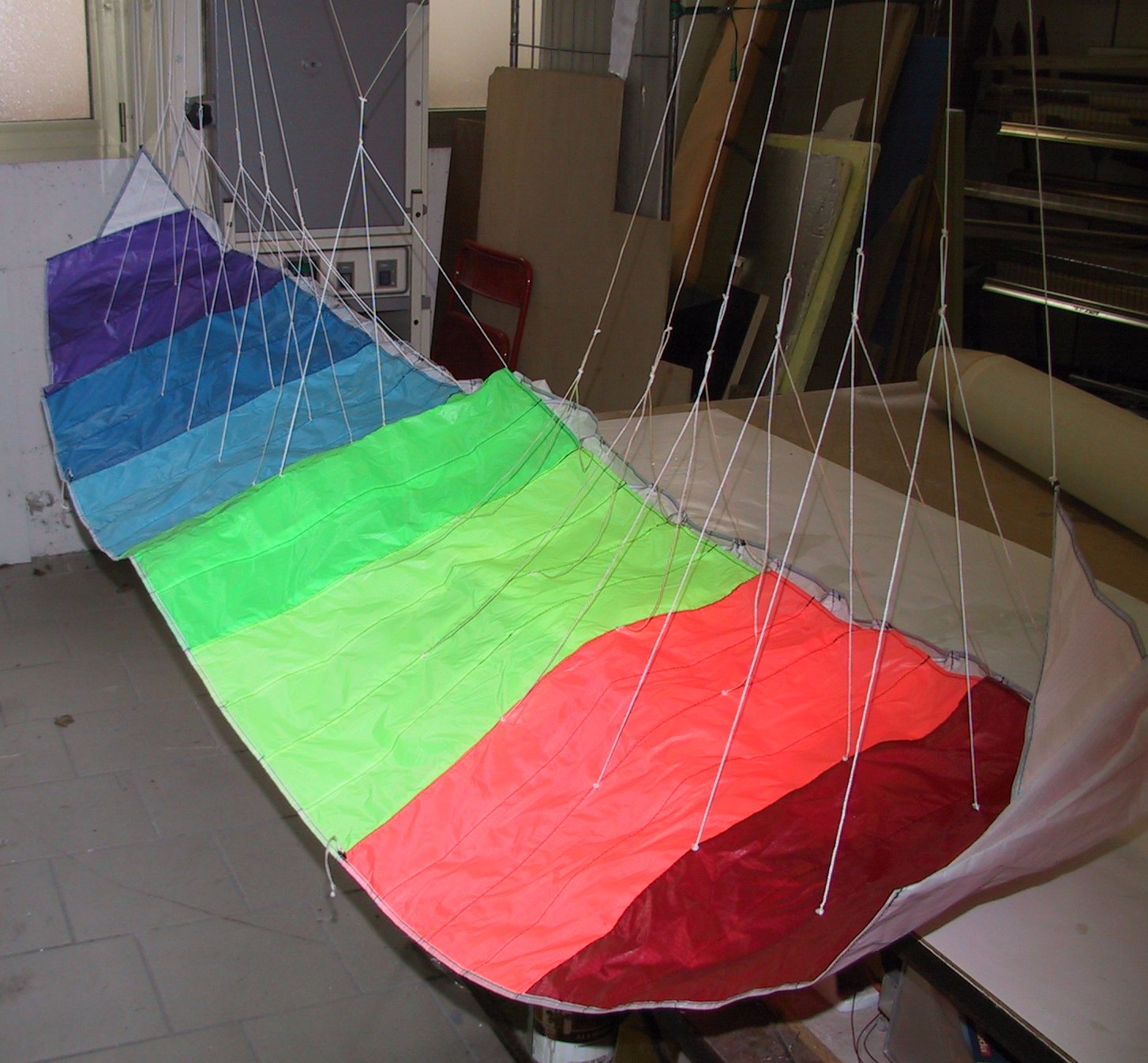
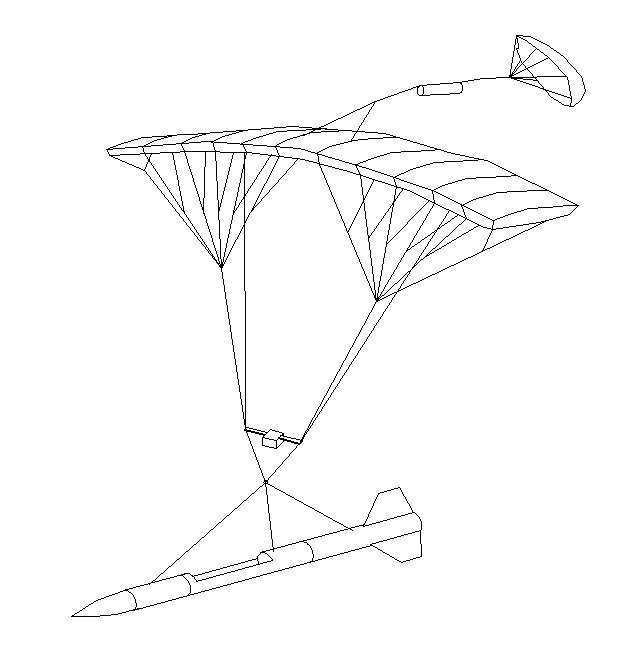
Il dispositivo di guida automatica
Parte 11 - L'AVIONICA E IL SISTEMA DI RADIOTELEMETRIA
La capsula payload e' composta da un cilindro in materiale composito multistrato ad alta resistenza.
Ospita un sofisticato equipaggiamento elettronico tra cui un datalogger per il profilo di volo, un datalink di trasmissione remota in UHF e un trasmettitore audio-video in banda 2400 Mhz.
La progettazione e costruzione ha richiesto molti mesi di lavoro, con un investimento economico notevole, ma il risultato finale e' stato adeguato alle aspettative.
L'airframe e' realizzato con un sandwich in tessuto di carbonio/kevlar-termanto-fiberglass, il tutto laminato con resina epoxy.
Il cono dell'ogiva e' invece realizzato con solo fiberglass in quanto ospita l'antenna di trasmissione UHF e il carbonio avrebbe ostacolato l'emissione radio.
Caratteristiche :
Diametro: 140 mm
Lunghezza totale : 850 mm
Massa solo cellula: 650 grammi
Massa equipaggiamento elettronico: 700 grammi
Massa totale: 1350 grammi
Materiale cellula: sandwich in tessuto carbonio/kevlar 220 gr/mq - termanto sp. 3 mm - fibra di vetro 120 gr/mq (esterno), il tutto laminato con resina epoxy.
Materiale ogiva: 3 strati di fibra di vetro da 120 gr/mq laminati con resina epoxy. Estremita' superiore e inferiore rinforzate con inserti in carbonio/kevlar.
Spessore parete cellula: 4 mm
Spessore parete ogiva: 1.2 mm
Equipaggiamento elettronico:
- Alimentazione: 11 celle NiCd 600 mA/h (tensione 13.2 Volt)
- Ricevitore radiocomando aeromodellistico a 7 canali, frequenza 40 Mhz, per il comando dell'espulsione di due paracadute e l'attivazione di due carichi elettrici (trasmettitori video e telemetria).
- Interruttore a due canali radiocomandato, con HEXFET di potenza, per l'alimentazione degli stadi finali dei trasmettitori UHF e SHF.
- Alimentatore stabilizzato multitensione con protezione dai sovraccarichi e cortocircuiti.
- Unita' centrale di elaborazione dotata di microcontroller PIC 16F876 a 20 Mhz, ingressi per 5 canali analogici, uscita seriale e display LCD. (vedi pagina dedicata)
- Unita' trasduttori ambientali con sensore barometrico Fujikura XFPM 155-KP e accelerometri Analog Device ADXL202 (a due assi) e ADXL150 (a singolo asse).
- Trasmettitore UHF (frequenza 433,65 Mhz) per dati digitali, potenza massima 500 mW.
- Trasmettitore SHF (frequenza 2440 Mhz) per segnali audio-video, potenza massima 200 mW.
- Microcamera a colori ad alta definizione, 420 linee, DSP (Digital Signal Processing) per una gestione ottimale delle prestazioni, obiettivo F3,6 .
- Microfono omnidirezionale ad alta sensibilita' per la trasmissione dell'audio al videoregistratore.
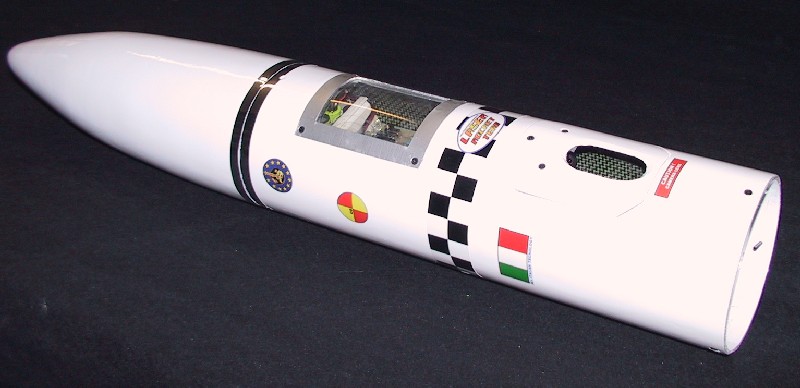
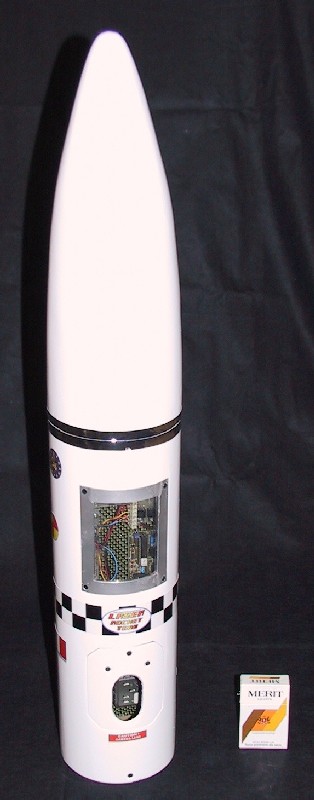
La capsula completa
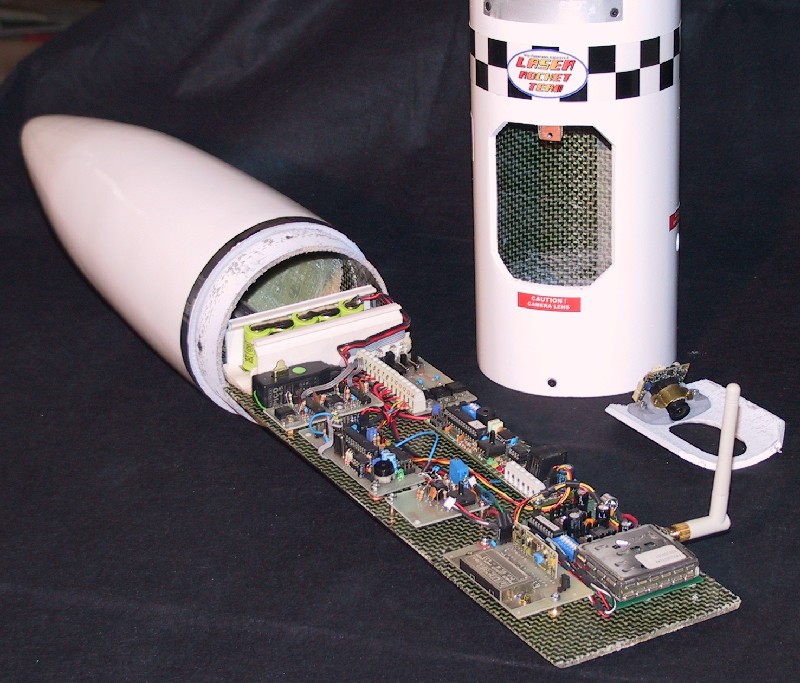
La piastra payload
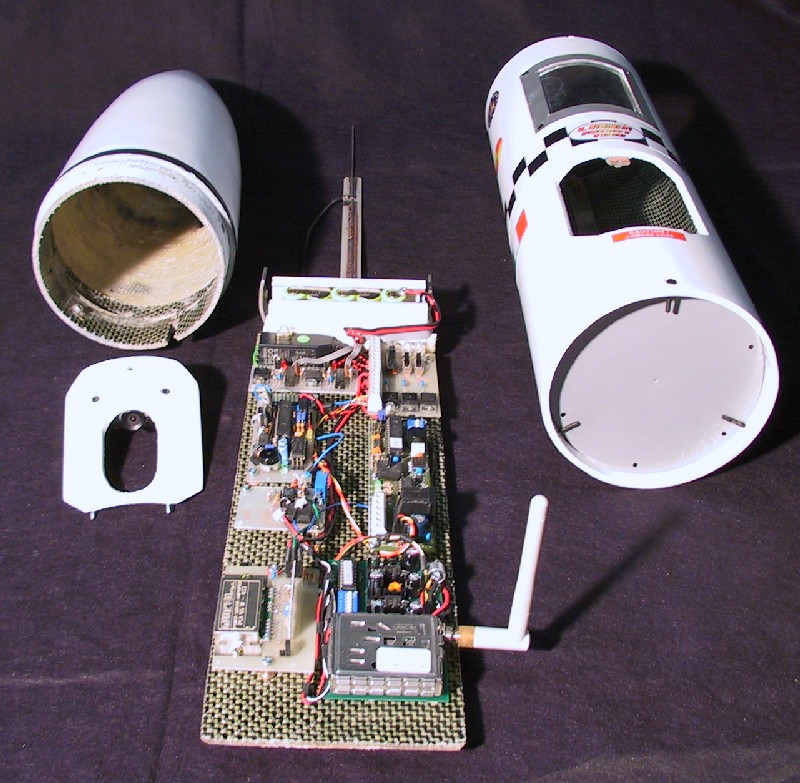
Componenti smontati
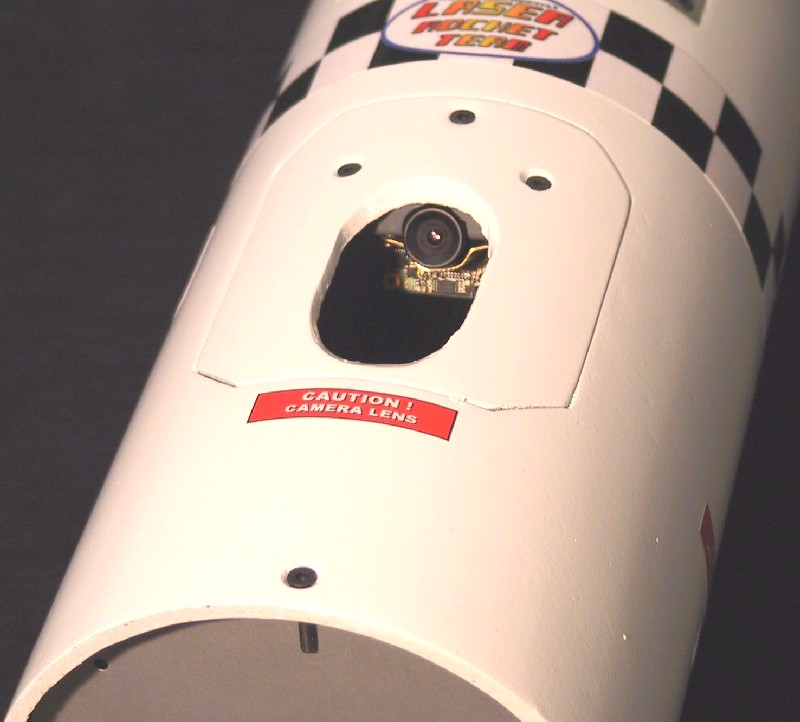
La videocamera
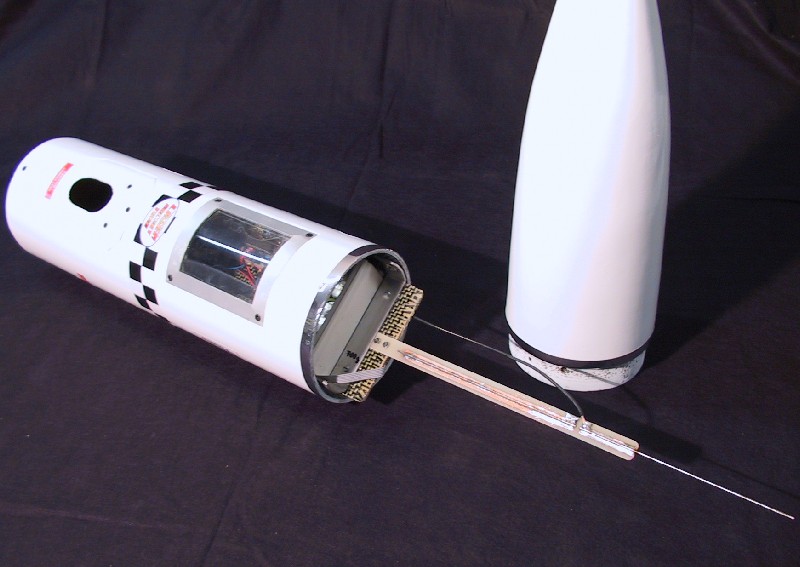
L'antenna UHF
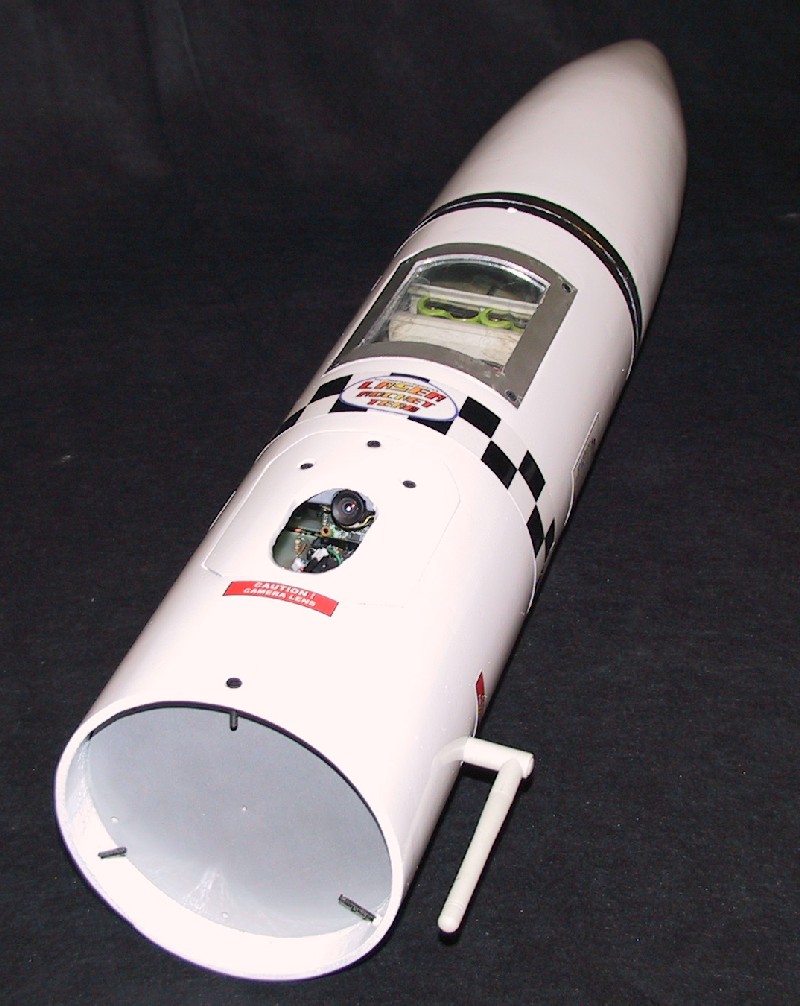
L'antenna SHF
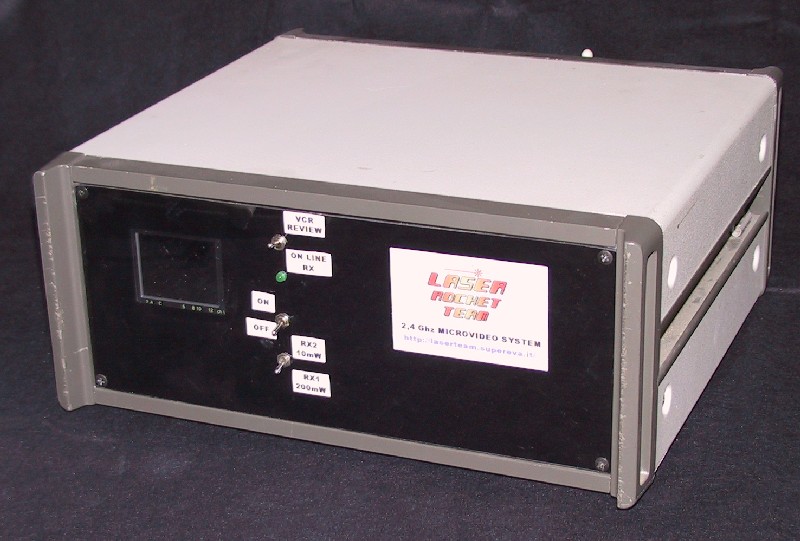
Il ricevitore video
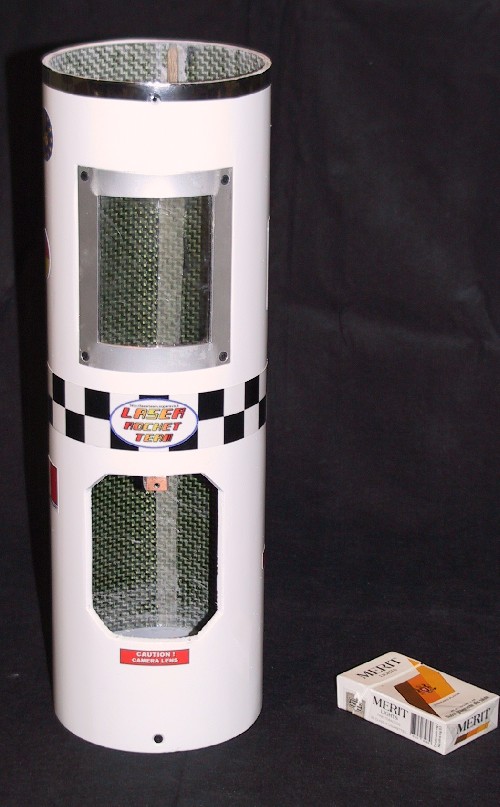
L'airframe
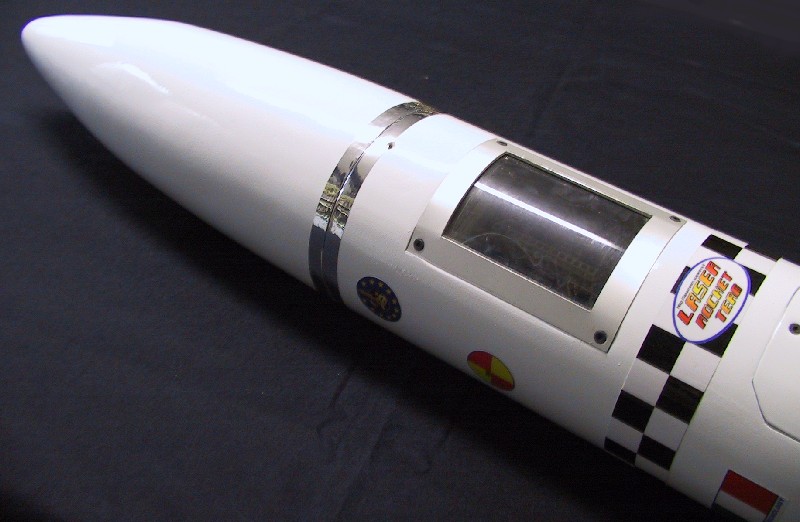
Lo sportello
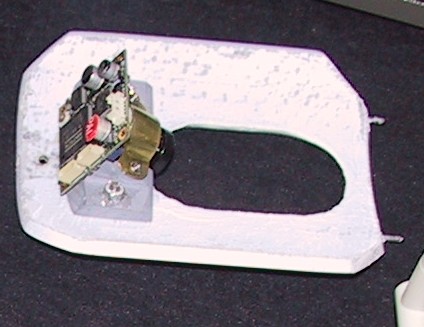
La videocamera
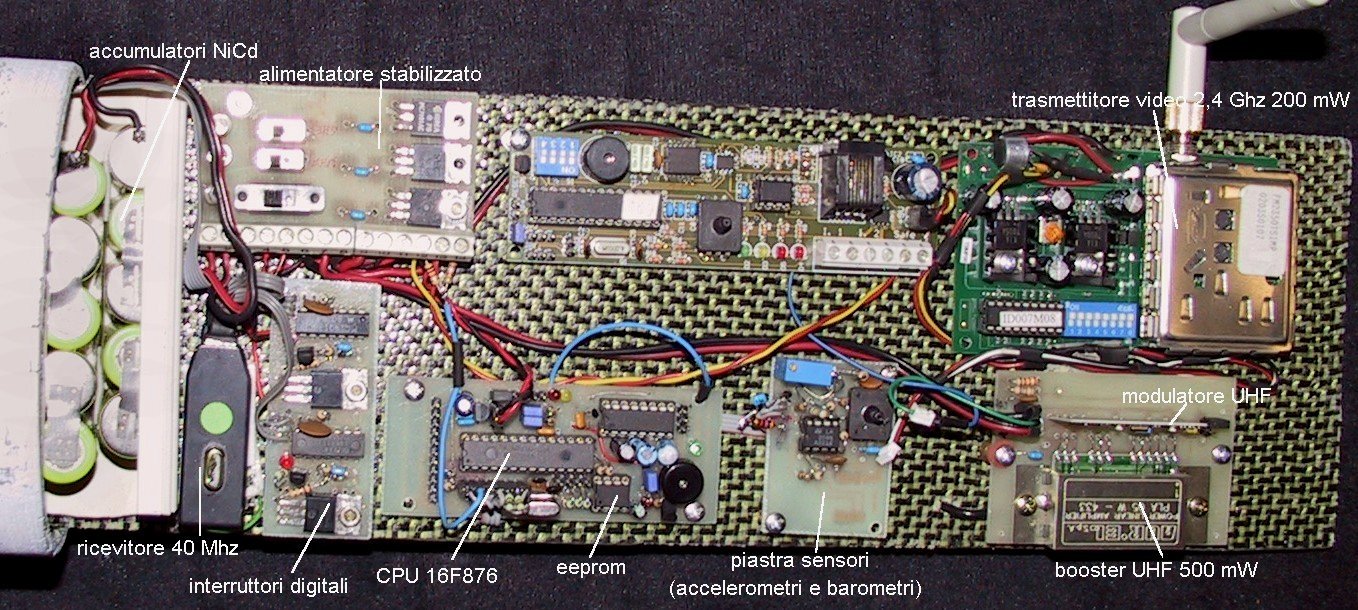
L'elettronica
Parte 13 - PROGETTO DELLA RAMPA DI LANCIO
Allo scopo di ottenere la migliore mobilita' e versatilita', la rampa di lancio del vettore Stratosfera e' prevista per essere installata a bordo di un carrello stradale di derivazione nautica, comunemente usati per il trasporto di imbarcazioni e gommoni. Il carrello e' a singolo asse, con portata massima di 800 Kg e dotato di gancio di traino standard.
La rotaia di scorrimento e' realizzata con una una guida in lega leggera ancorata ai tronchoni di traliccio da 2 metri, per un totale di 10 metri nella configurazione completa.
E' prevista anche una configurazione ridotta con un numero inferiore di sezioni installate.
Le sezioni sono assemblate ad incastro al momento della messa in opera.
Al centro del pianale e' fissato uno snodo al quale e' collegata la prima sezione del traliccio in modo da montare la rotaia orizzontalmente.
A montaggio terminato e vettore posizionato sulla rotaia, la rampa viene sollevata in posizione verticale per mezzo di un verricello elettromeccanico oppure un pistone idraulico.
Le controventature realizzate in tubolare irrigidiscono la struttura riducendo le flessioni laterali e le vibrazioni.
Il pianale e' attrezzato per contenere le sezioni del traliccio durante il trasporto ed inoltre alla sua base e' installata la bombola dell'ossidante.
Sulla parte sottostante alla rampa e' costruito un deflettore per i gas di scarico, adeguatamente protetto dalle alte temperature con un rivestimento di materiale refrattario.
A corredo della rampa e' prevista l'installazione di alcune casse metalliche per contenere attrezzi ed accessori di montaggio.
.gif)
Vista laterale
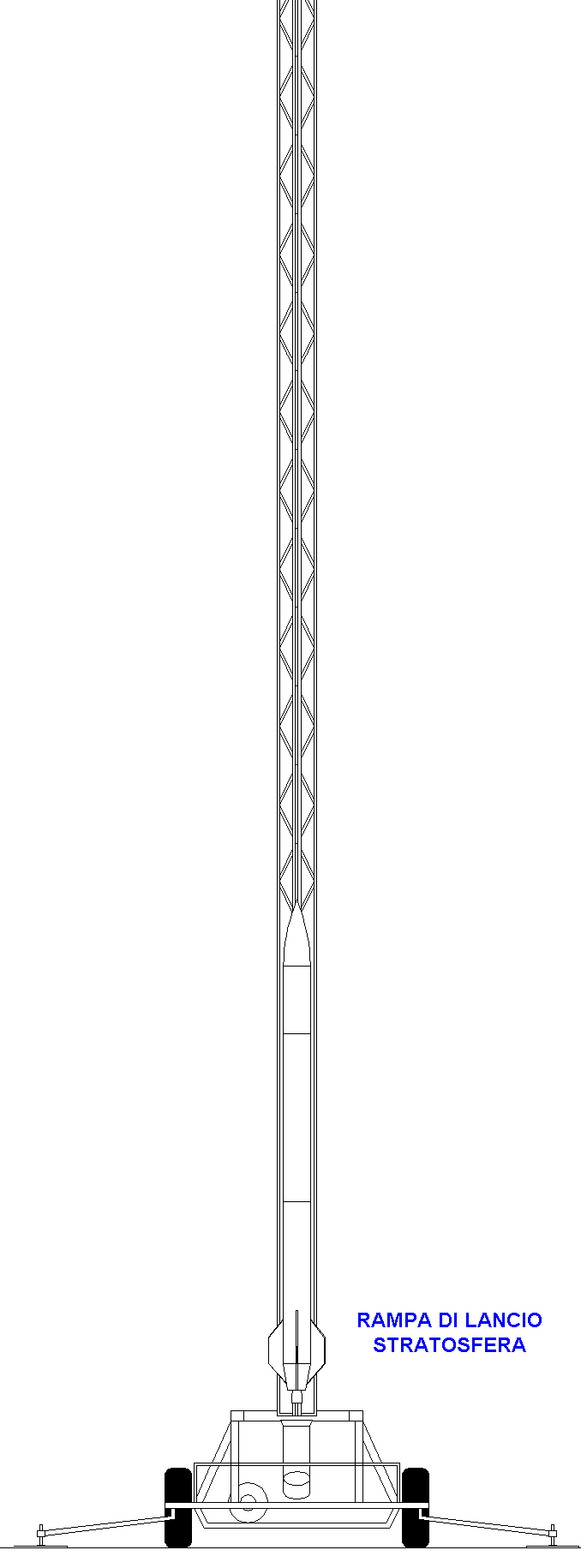
Vista posteriore
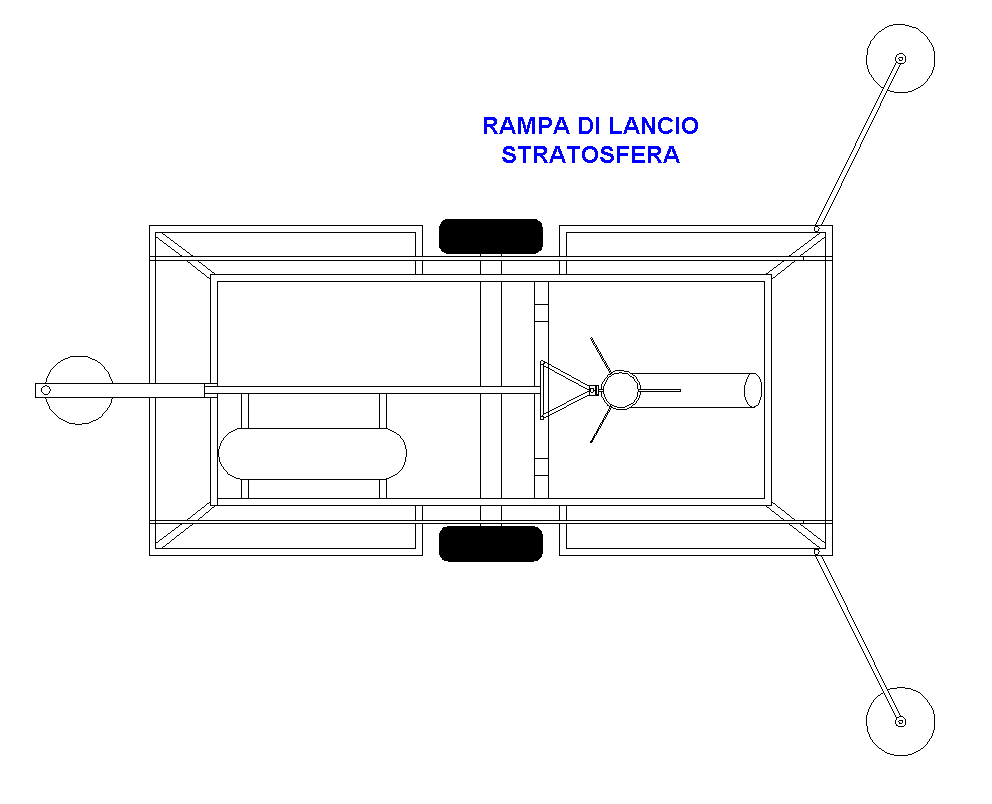
Vista da sopra