STRATOS, stampante 3D
Come costruire una stampante 3D con componenti di recupero.
21/02/2015
Stampante 3D... parola che ultimamente si sente anche troppo spesso in TV, giornali, riviste ed ovviamente in rete... spesso a sproposito e senza cognizione di causa.
Io ho iniziato la mia avventura su questo tema circa quattro anni fa, in tempi non sospetti, e da allora ho accumulato una certa esperienza realizzando (e disfando) almeno cinque esemplari diversi.
Poichè l'oggetto in questione sembra suscitare inconfessabili istinti di possesso, credo che molti siano interessati alla sua costruzione.
Ma da dove partire? Lo compro già pronta o posso tentare di farmela in casa?
Meglio un kit o uno scratch fatto con pezzi assortiti presi dai cassetti del laboratorio?
Che struttura meccanica scegliere e quali motori ed elettronica posso utilizzare?
Per rispondere a queste domande ho scritto questo tutorial, sperando possa essere utile a chi fosse interessato alla costruzione dell'agognato strumento.
La tecnologia della stampa 3D comprende diverse varianti, da quella più semplice ad estrusione di polimero plastico, a quelle più sofisticate (foto polimerizzazione UV), con laser o proiettore DLP. In questo tutorial tratterò solo delle stampanti 3D di tipo amatoriale, basate sull'estrusione di polimeri plastici, una tecnologia chiamata FDM (Fused Deposition Modeling).
E' una scelta obbligata per la relativa semplicità costruttiva, sull'economicità, per la versatilità, ingombro limitato e disponibilità di componenti commerciali dedicate a costi abbordabili.
Per contro, con questa famiglia di stampanti la produzione è limitata a piccole serie, dato il lungo tempo necessario.
Inoltre, per la natura stratificata del materiale, l'aspetto superficiale del pezzo sarà piuttosto irregolare.
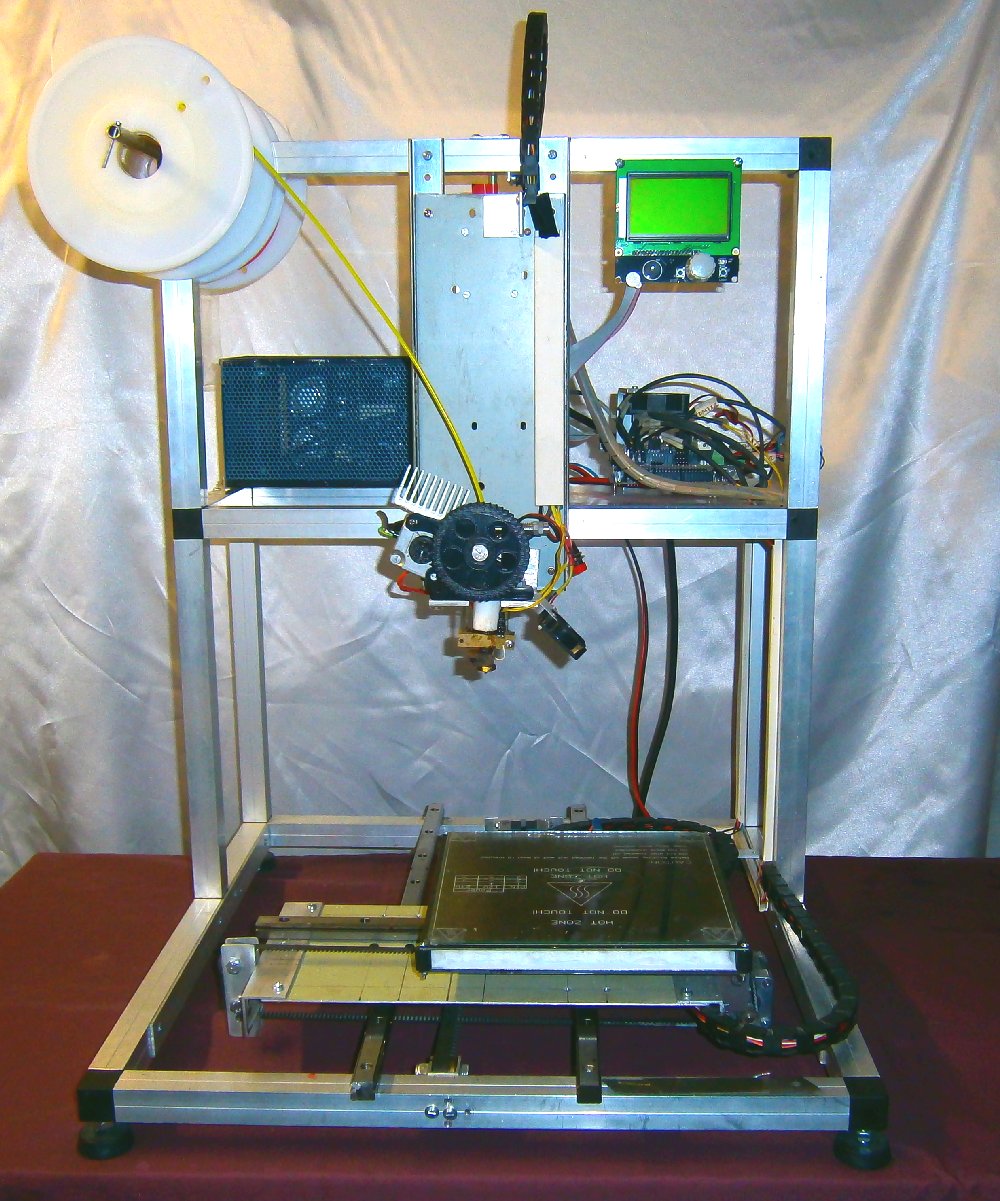
Stampanti autoreplicanti.
No, non sto citando Blade runner. Le hanno chiamate "autoreplicanti" perchè di fatto una stampante 3D è in grado di realizzare molti dei componenti necessari per realizzare un'altra stampante.
In realtà la stessa cosa si potrebbe dire per una fresa CNC, anche se nessuno ha mai osato definire "autoreplicante" un centro di lavoro.
Immagino che la definizione sia nata per motivi di propaganda, anche perchè sarebbe applicabile solo ad una certa famiglia di stampanti, costruite con un'accrocco di barre filettate (Darwin, Prusa, Mendel ecc.), che caratterizzano i modelli più semplici ed economici.
Pur nella loro semplicità, questi modelli sono perfettamente funzionanti e sono considerati "l'entry level" per i principianti.
In realtà la stessa cosa si potrebbe dire per una fresa CNC, anche se nessuno ha mai osato definire "autoreplicante" un centro di lavoro.
Immagino che la definizione sia nata per motivi di propaganda, anche perchè sarebbe applicabile solo ad una certa famiglia di stampanti, costruite con un'accrocco di barre filettate (Darwin, Prusa, Mendel ecc.), che caratterizzano i modelli più semplici ed economici.
Pur nella loro semplicità, questi modelli sono perfettamente funzionanti e sono considerati "l'entry level" per i principianti.
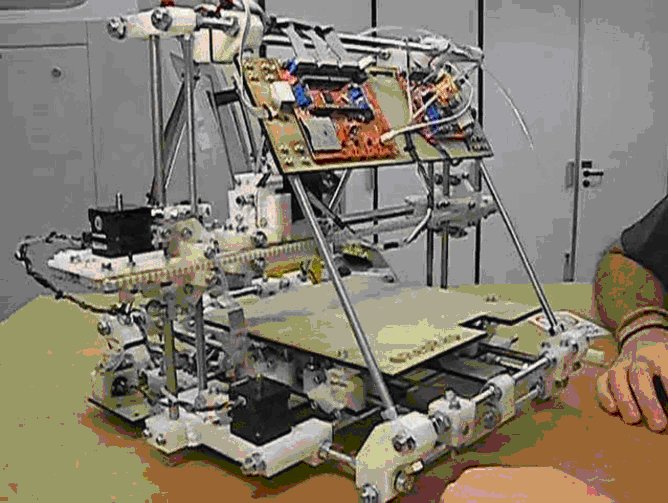
In seguito descriverò il mio prototipo, che "deraglia" notevolmente da questi classici canoni costruttivi e che ha avuto come risultato una struttura meno ingarbugliata ed esteticamente meno rudimentale.
Iniziamo con descrivere di cosa si tratta e a cosa serve una 3D printer: Una macchina di questo tipo è molto simile ad una fresa CNC controllata da computer. La differenza sostanziale sta nel fatto che una fresa CNC produce il pezzo desiderato per asportazione di materiale a partire da un blocco compatto.
Il movimento degli assi X e Y portano la fresa nei punti dove deve essere asportato il materiale mentre l’abbassamento dell’asse Z permette l’asportazione di strati di materiale sempre più profondi.
La stampante 3D invece produce il pezzo finito per aggiunta di materiale, in strati successivi, a partire dalla base e via via proseguendo verso l’alto. La macchina sovrappone sottili immagini bidimensionali che vanno a costruire verticalmente un oggetto solido.
Qualsiasi oggetto? No, almeno non tutti quelli ipotizzati da certi giornalisti entusiasti (e disinformati).
Il mitico fischietto lo stampa, come altri oggettini di piccolo conto come vasetti, portagioielli, gadget, ornamenti, portapenne ecc.
Quello che per ora non si possono fare sono gli oggetti di altissima precisione, quelli con particolari caratteristiche di resistenza meccanica, termica o soggetti ad usura. Ciò non impedisce invece di realizzare componenti strutturali, ingranaggi, meccanismi anche di una certa complessità, stampi per colata di resine da cui ricavare dei positivi, oppure positivi per la fusione a cera persa.
Ma la vera specialità delle stampanti 3D è quella di poter realizzare "pezzi impossibili" come ad esempio oggetti all'interno di altri oggetti (classico esempio il cuscinetto a sfere stampato in un colpo solo).
Come funziona?
Per prima cosa è necessario realizzare un disegno tridimensionale usando un'opportuno software CAD, salvandolo in formato STL (Standard Triangulation Language), usato come standard in questo tipo di applicazione.
Un esempio di CAD freeware è Sketchup, che richiede però uno script esterno per il salvataggio in formato STL.
Per i primi esperimenti si possono anche scaricare gratuitamente dalla rete migliaia di oggetti pronti, anche se non sempre personalizzabili, vedi ad esempio il sito : www.thingiverse.com
In seguito il disegno viene "affettato" tramite software specifici.
Io uso "Cura" della ditta Ultimaker, che potete trovare qui: https://software.ultimaker.com/
Consiste in un processo software che parte da un reticolo di triangoli che compongono la superficie dell’oggetto 3D, lo trasforma in una serie di sezioni orizzontali, elabora l’immagine bidimensionale e converte ogni segmento in un linguaggio specifico chiamato G-CODE (molto simile a quello usato nelle macchine a controllo numerico).
Tale linguaggio viene poi trasferito opportunamente alla stampante tramite interfaccia USB oppure (se è presente l'apposito lettore), su scheda SD.
Questo sistema è molto comodo perchè rende autonoma la stampante, senza la necessità di collegare il computer durante la stampa.
Il firmware del controller della stampante interpreta i comandi GCODE trasformandoli in spostamenti dei motori stepper (assi X e Y) e dell’estrusore (asse Z). Lo stesso codice imposta anche l'azzeramento automatico iniziale, la temperatura dell'estrusore, dell'eventuale piatto riscaldato e delle eventuali ventole di raffreddamento.
Un esempio di CAD freeware è Sketchup, che richiede però uno script esterno per il salvataggio in formato STL.
Per i primi esperimenti si possono anche scaricare gratuitamente dalla rete migliaia di oggetti pronti, anche se non sempre personalizzabili, vedi ad esempio il sito : www.thingiverse.com
In seguito il disegno viene "affettato" tramite software specifici.
Io uso "Cura" della ditta Ultimaker, che potete trovare qui: https://software.ultimaker.com/
Consiste in un processo software che parte da un reticolo di triangoli che compongono la superficie dell’oggetto 3D, lo trasforma in una serie di sezioni orizzontali, elabora l’immagine bidimensionale e converte ogni segmento in un linguaggio specifico chiamato G-CODE (molto simile a quello usato nelle macchine a controllo numerico).
Tale linguaggio viene poi trasferito opportunamente alla stampante tramite interfaccia USB oppure (se è presente l'apposito lettore), su scheda SD.
Questo sistema è molto comodo perchè rende autonoma la stampante, senza la necessità di collegare il computer durante la stampa.
Il firmware del controller della stampante interpreta i comandi GCODE trasformandoli in spostamenti dei motori stepper (assi X e Y) e dell’estrusore (asse Z). Lo stesso codice imposta anche l'azzeramento automatico iniziale, la temperatura dell'estrusore, dell'eventuale piatto riscaldato e delle eventuali ventole di raffreddamento.
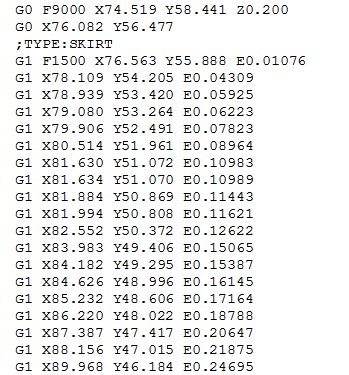
Esempio di G-code
Per vari motivi, non ultimo per la mia filosofia di riciclatore di componenti usati, ho optato per la costruzione casereccia, sfruttando fino all'ultimo rimasuglio presente nel mio laboratorio.
Per le parti strettamente specializzate ho dovuto arrendermi all'acquisto di componenti commerciali. Infatti i primi tentativi di realizzare un estrusore, senza disporre di speciali strumenti, sono stati purtroppo un fallimento.
Per la parte elettronica, data la complessità della scheda, non era molto intelligente tentare di progettarla in casa, inoltre dato il costo ormai ragionevole era più conveniente acquistarla in kit, completa di circuito stampato e componenti.
Il montaggio ha richiesto circa 6 ore e non vi sono stati problemi.
La scheda Arduino ATmega non necessita di commenti, si trova dappertutto a prezzi simili.
La configurazione meccanica
La meccanica degli assi X e Y è simile a quella di una CNC, mentre l’asse Z lavora al contrario, partendo dal basso e salendo man mano che il pezzo viene formato.
Esistono diverse configurazioni meccaniche, io ho scelto la più semplice ed a mio avviso la più affidabile e funzionale: il piatto di stampa è mobile sui due assi orizzontali X eY, mentre l'estrusore (asse Z), si muove solo in verticale.
Altre soluzioni prevedono invece che il piatto di stampa si muova solo su un asse, mentre l'estrusore usi gli altri due assi.
La configurazione "DELTA" prevede addirittura che il piatto di stampa sia fisso e l'estrusore si muova su tutti e tre gli assi.
Tutti gli assi scorrono su apposite guide scorrevoli, generalmente composte da cuscinetti cilindrici a ricircolo di sfere, o meglio ancora da slitte a ricircolo di sfere. I movimenti sono generati da motori stepper (passo passo) classe NEMA 17 o 23 dotati di pulegge e cinghie dentate per trasferire il moto ai carrelli mobili.
La costruzione deve essere precisa per garantire l'indispensabile accuratezza. Non sono consentiti giochi o laschi per non compromettere la definizione del pezzo creato e gli attriti devono essere ridotti al minimo.
Esistono diverse configurazioni meccaniche, io ho scelto la più semplice ed a mio avviso la più affidabile e funzionale: il piatto di stampa è mobile sui due assi orizzontali X eY, mentre l'estrusore (asse Z), si muove solo in verticale.
Altre soluzioni prevedono invece che il piatto di stampa si muova solo su un asse, mentre l'estrusore usi gli altri due assi.
La configurazione "DELTA" prevede addirittura che il piatto di stampa sia fisso e l'estrusore si muova su tutti e tre gli assi.
Tutti gli assi scorrono su apposite guide scorrevoli, generalmente composte da cuscinetti cilindrici a ricircolo di sfere, o meglio ancora da slitte a ricircolo di sfere. I movimenti sono generati da motori stepper (passo passo) classe NEMA 17 o 23 dotati di pulegge e cinghie dentate per trasferire il moto ai carrelli mobili.
La costruzione deve essere precisa per garantire l'indispensabile accuratezza. Non sono consentiti giochi o laschi per non compromettere la definizione del pezzo creato e gli attriti devono essere ridotti al minimo.
I materiali da stampa generalmente usati
Nelle stampanti casalinghe si usano sostanzialmente due tipi di polimeri termoplastici:
1) Il PLA (acido polilattico) è un polimero termoplastico biodegradabile (usato anche nei nuovi shopper della spesa). E' ricavato dal mais e fonde a circa 185/190 gradi, il piano di stampa deve essere regolato a 60 gradi.
2) L'ABS (acrilonitrile-butadien-stirolo) è un polimero composto dai tre componenti che formano il suo nome, fonde ad una temperatura di 230 gradi.
Meccanicamente è più robusto del PLA, il che giustifica il suo impiego. Inoltre non essendo biodegradabile ha una stabilità migliore agli agenti atmosferici. Il piatto di stampa va regolato a 110 gradi.
Entrambi i materiali sono disponibili in commercio in bobine di varie metrature e colori.
Gli spessori standard sono da 3 mm e 1,75 mm, dunque occorre scegliere lo spessore in base al diametro di entrata dell'estrusore.
La rete consente un'estesa reperibilità, con offerte di centinaia di distributori.
Il cuore della stampante 3D, l'estrusore
L'estrusore è un dispositivo studiato per riscaldare un filo di materiale plastico per ottenere un filamento fuso dello spessore di 0,35 mm o 0,5 mm che viene depositato sul piatto di stampa in spessori successivi.
A prescindere dallo spessore del filamento, generalmente lo strato è spesso 0,2/0,3 mm in modo da riempire bene lo spazio circostante.
Ne risulta che per ottenere un millimetro di spessore-oggetto, servono cinque passaggi (o strati).
Una volta realizzata la stampante è possibile stamparsi in proprio i componenti degli estrusori, da utilizzare su un'altra stampante.
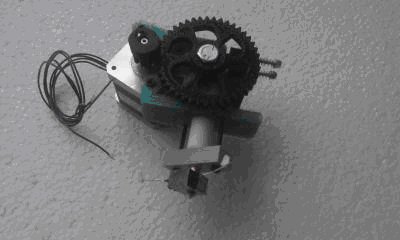
Estrusore Wade's Modello base
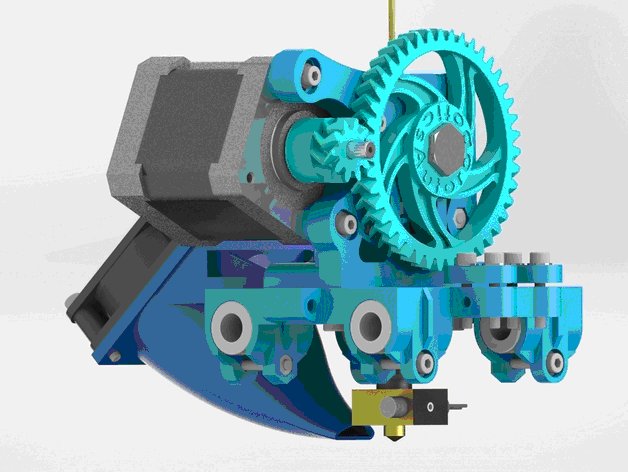
Altro estrusore Wade. Creditis: http://www.thingiverse.com/thing:347610
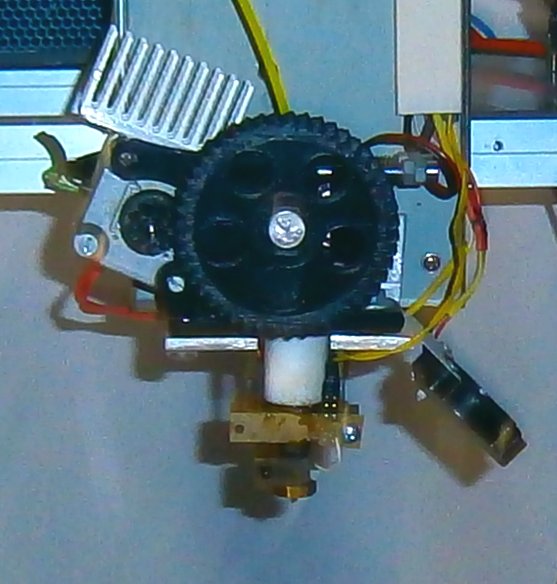
Il mio estrusore
L'estrusore è composto da un motore stepper che per mezzo di adeguate riduzioni fa girare un perno goffrato su cui è premuto il filamento plastico. Girando, lo spinge in un cilindretto in teflon che termina con una "camera calda" dove viene fuso.
All'estremità inferiore della camera calda (Hot end) c'e' un ugello che lo trasforma in un filamento sottile.
La temperatura dell'Hot end deve essere mantenuta costante ad una temperatura prestabilita (circa 190 gradi per il PLA e 220 per l'ABS).
Il riscaldamento è prodotto da un resistore elettrico inserito nell'Hot end, monitorizzato costantemente da un termistore in vetro interfacciato alla scheda di controllo.
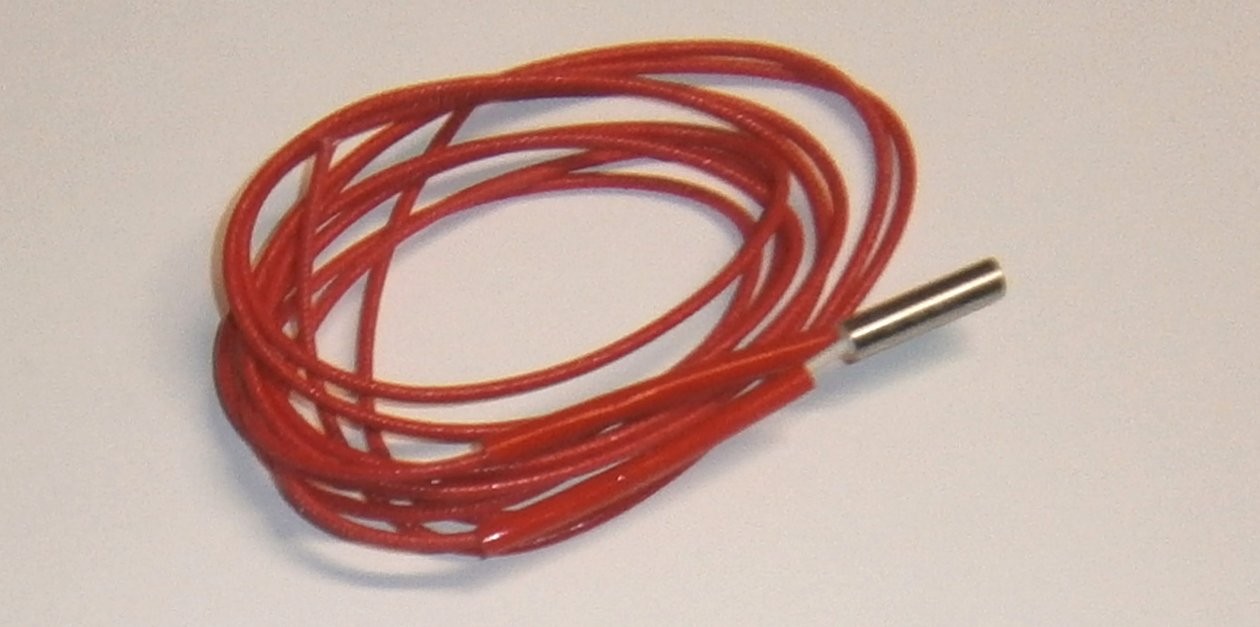
Resistore corazzato per il riscaldamento dell'Hot End
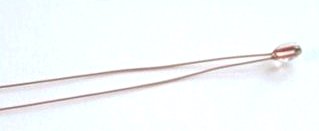
Termistore NTC in vetro da 100KOhm
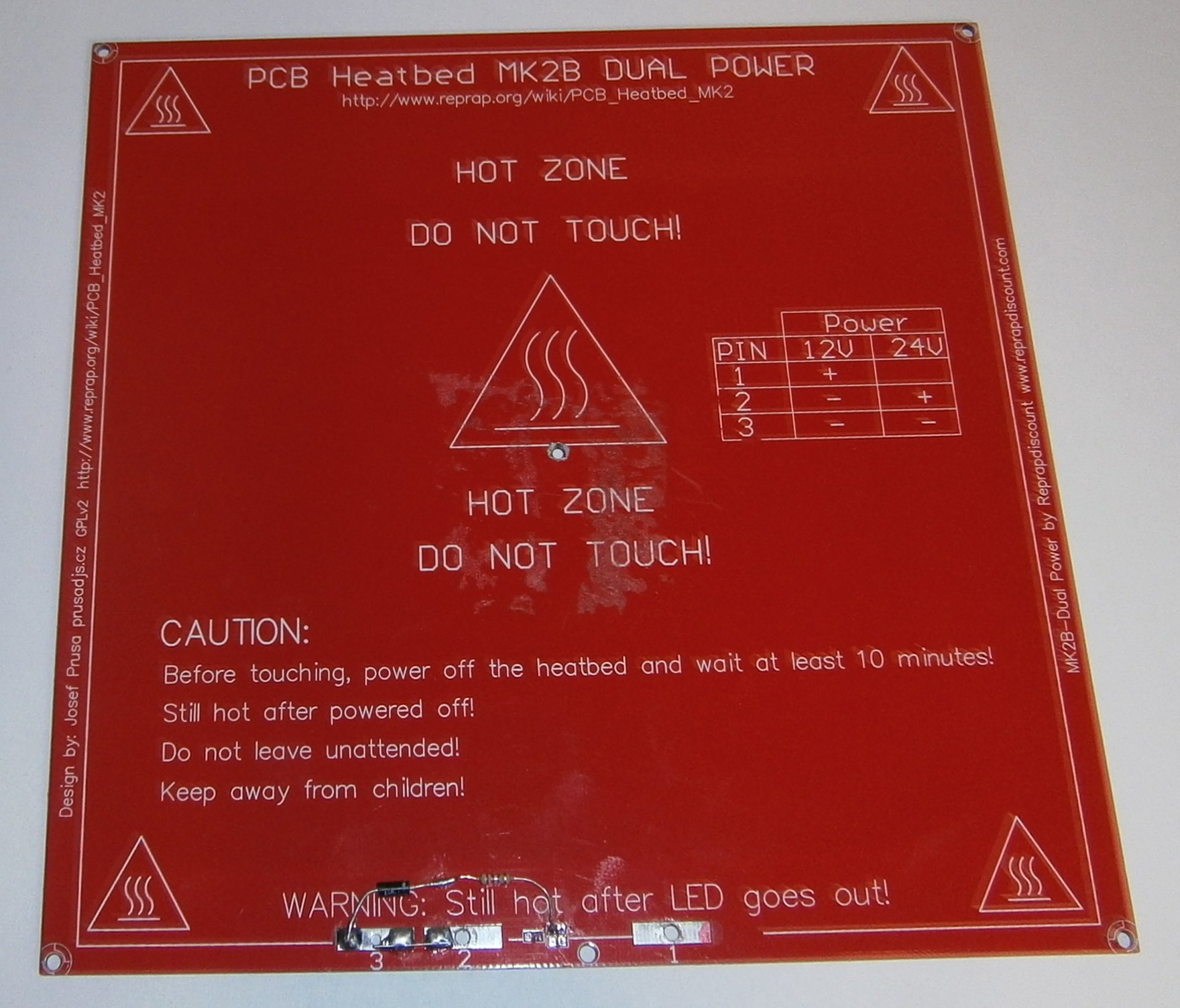
Il piatto di stampa (Heat bed)
Nelle prime stampanti 3D si usava un supporto qualsiasi: (allumino, vetronite ecc.). Nasceva però un problema serio: l'adesione era precaria e durante la stampa il pezzo si staccava o spostava. Questo ovviamente comprometteva l'intero lavoro.
Per migliorare l'adesione sono stati adottati i piatti di stampa riscaldati, che sono realizzati in due modi: con delle resistenze corazzate fissate ad un piatto di alluminio, oppure un circuito stampato in vetronite con incisa una rete resistiva in rame, calibrata per funzionare a 12 o 24 Volt con un assorbimento di una decina di ampere.
La temperatura di lavoro va dai 60 ai 110 gradi in funzione del materiale di stampa. Sopra la base riscaldante viene fissato un vetro al borosilicato resistente al calore.
Al termine della stampa, quando il piatto si raffredda, il pezzo si stacca facilmente per merito del restringimento termico.
Io ho anche l'abitudine di spruzzare un sottile velo di lacca per capelli sul piatto, per migliorare l'adesione.
I motori stepper
Non credo sia necessaria una trattazione approfondita, nell'elettromeccanica sono usati ovunque. Nella mia stampante sono stati installati dei NEMA17, che non è la marca, bensì la classe di dimensione.
A titolo informativo hanno il lato di 43 mm (1,7 pollici, appunto) e profondità 34 mm. Sono dei motori bipolari (a due bobine) prodotti dalla Sainsmart e siglati 42HSC1406-25. Lo step base è di 1,8 gradi, dunque 200 passi/giro.
In realtà vanno bene anche altri motori della stessa classe, compresi quelli di recupero.
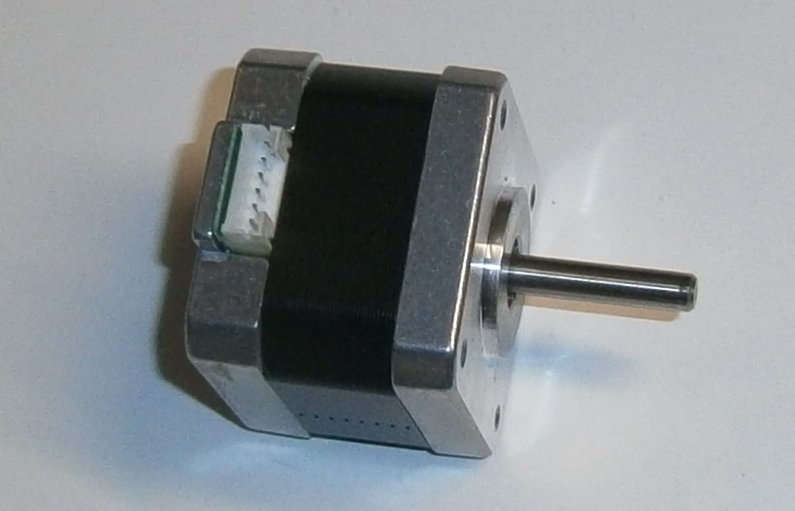
Motore stepper classe Nema17
L'elettronica di controllo
Quasi tutte le stampanti sono dotate di un controllore basato sull'onnipresente Arduino, corredato di uno shield dedicato.
In commercio ce ne sono diversi: ad esempio la scheda Sanguinololu, la Ramps ecc.

Controller monoscheda Sanguinololu
Dopo varie esperienze con la scheda Sanguino ho preferito passare alla Ramps 1.4, per questioni di maggiori prestazioni ed espandibilità, tra cui la possibilità di montare un secondo estrusore per stampe a due colori.
Questa scheda è in realta una "shield" da applicare sopra una scheda "All In One" Arduino ATMega, che è dotata di un processore ATMega 2560 che offre 54 pin di IN/OUT, 16 ingressi analogici, 4 UART, una porta USB e un header ICSP.
Qui trovare le specifiche tecniche: arduino.cc/en/Main/ArduinoBoardMega2560
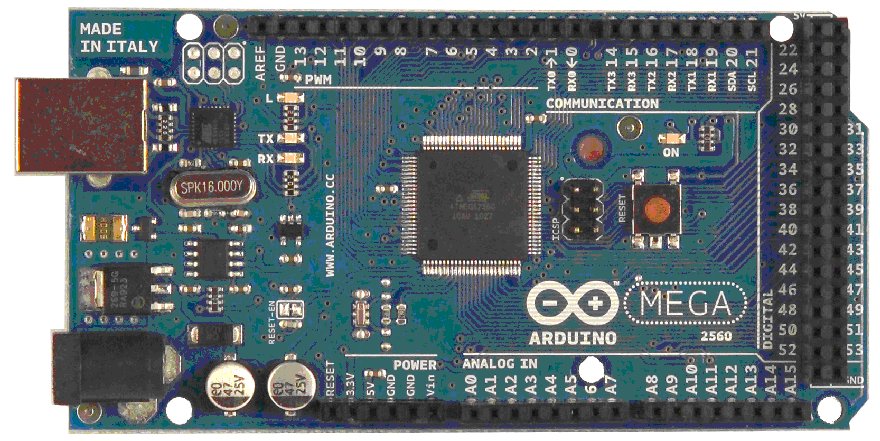
Arduino Mega ADK 2560 (fonte sito Arduino)
La shield Ramps 1.4 è impilabile (pin to pin) direttamente sulla scheda Arduino e completa i dispositivi di interfaccia in modo da avere tutto il necessario in unico blocco. A bordo della shied sono infatti presenti cinque zoccoli predisposti per i moduli di potenza per il controllo dei motori stepper, chiamati Step Stick.
La shield dispone inoltre di due uscite per gli Hotend, un'uscita per l'Hotbed, tre ingressi per i termistori di controllo temperatura, tre ingressi per i finecorsa (End stop), l'interfaccia per un display grafico 12864, l'interfaccia per un lettore di schede SD e un encoder per navigare sui vari menu.
Qui trovate lo schema, disposizione dei componenti, master del CS: http://reprap.org/wiki/Marlin
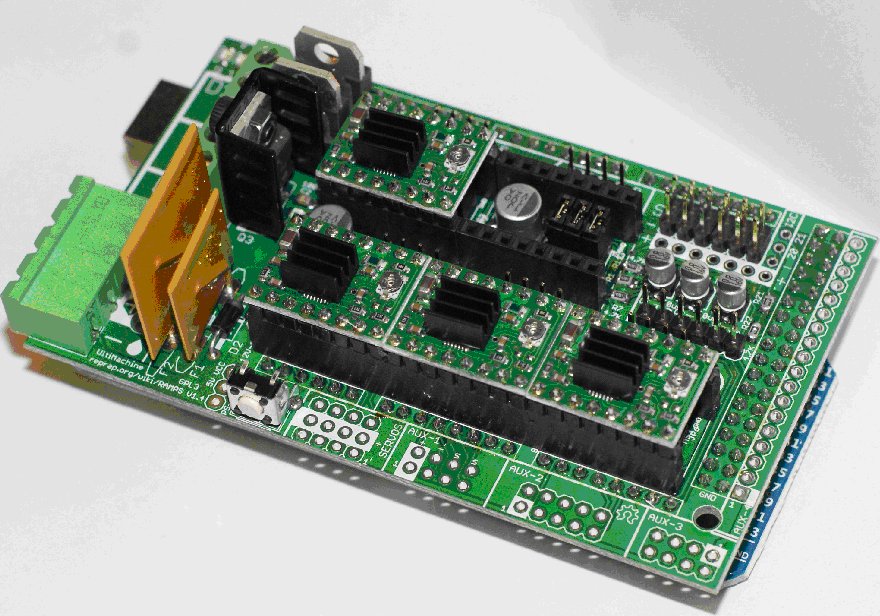
Schede Ramps 1.4 (Fonte sito RepRap)
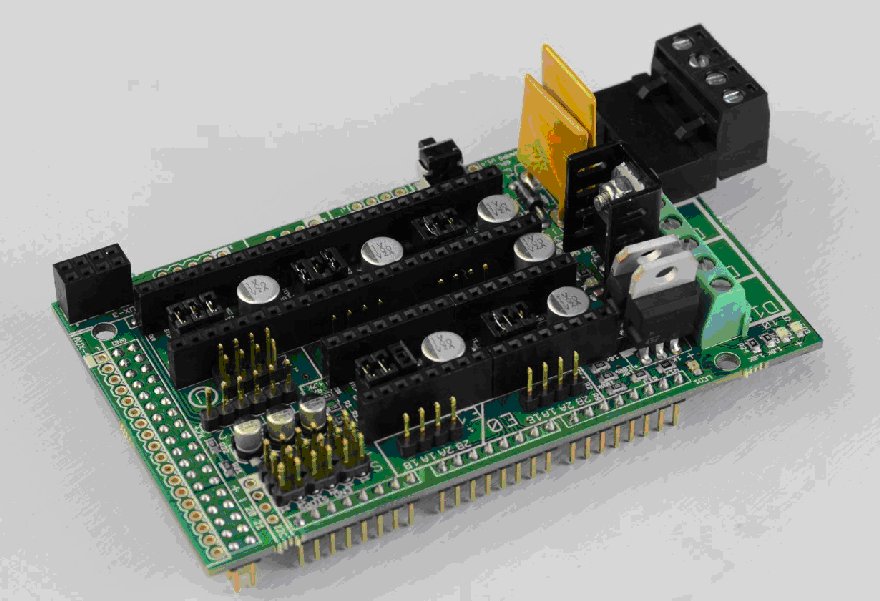
Per i dettagli del display LCD grafico date un'occhiata qui: reprap.org/wiki/RepRapDiscount_Full_Graphic_Smart_Controller
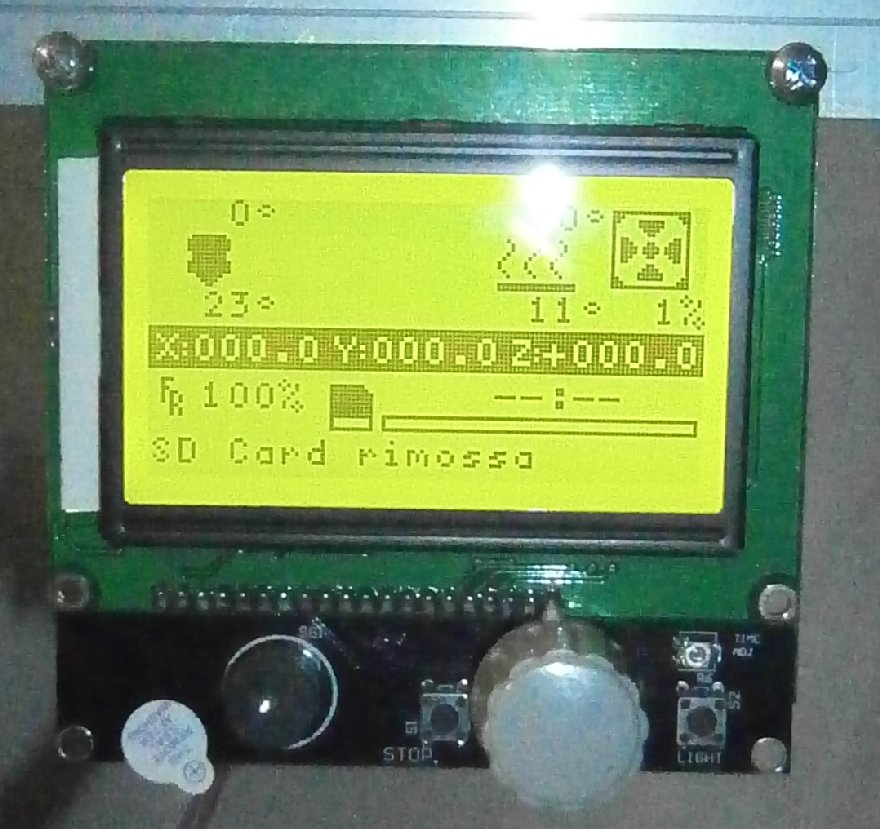
Display LCD grafico 12864 con encoder e lettore schede SD
I driver per i motori stepper (Step Stick)
I più noti sono quelli costruiti dalla Pololu, dotati del chip A4988, che sono sostanzialmente dei driver stepper dotati di micropasso e feedback della corrente assobita (max 2A). In una schedina di pochi millimetri di lato che comprende tutto il necessario per pilotare con estrema precisione i motori stepper.
La definizione massima è di un sedicesimo di passo, dunque per ogni giro potremo ottenere 3200 passi. La corrente è facilmente regolabile con un micro trimmer presente sulla scheda, da 0 a 2 Ampere.
Qui potete trovare le specifiche tecniche ed altre info: reprap.org/wiki/StepStick
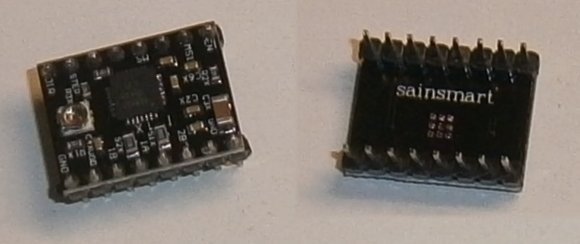
StepStick tipo Pololu
Lista dei materiali per la parte elettromeccanica
4 motori stepper Nema 17 (o Nema 23) da 200 passi/giro,
4 pulegge dentate diametro 14mm passo T10,
2 metri di cinghie dentate compatibili con le pulegge,
3 microswitch di fine corsa (endstop),
1 arduino ADK Mega2560,
1 shield Ramps 1,4,
4 Step Stick Pololu (stepper motor driver),
4 alette di raffreddamento per i Pololu,
1 pannello LCD 12864 completo di lettore scheda SD,
3 ventole 40x40,
1 lastra di vetro borosilicato 220x220 mm,
1 set cavi di collegamento motori, sensori e finecorsa,
1 cavo USB tipo stampante
In rete si trovano Kit completi del materiale sopraelencato per circa 260 euro
Ci serviranno inoltre:
1 estrusore completo di Hot end, tipo Wade extruder,
1 resistenza riscaldante corazzata per l'estrusore, da 6,8 Ohm 6W,
2 termistori NTC da 100 KOhm in vetro
I prezzi del materiale sopraelencato variano dai 60 ai 100 euro
Ci servirà anche un alimentatore stabilizzato a 12V da almeno 250W (20/25 Ampere).
Sembrano troppi ma tra Hotbed e Hotend gli ampere assorbiti sono tanti, senza contare i motori. Volendo è possibile sdoppiare le alimentazioni usando due alimentatori, uno per la sezione elettronica ed uno per la sezione di potenza.
Lista dei materiali per la parte strutturale
Vediamo dunque come ho realizzato la mia stampante, battezzata "Stratos" (chissà perchè...).
Per la struttura base ho impiegato dei profilati quadri in alluminio in vendita presso i vari Brico, che solitamente vengono venduti per la costruzione di scaffalature personalizzate. Oltre alle verghe si trovano anche i raccordi in plastica di vario tipo.
Servono questi pezzi di profilo a sezione quadrata di alluminio da 24x24 mm che potrete farvi tagliare direttamente nell'officina del Brico:
4 pezzi lunghi 16 cm,
2 pezzi lunghi 28 cm,
5 pezzi lunghi 46 cm,
4 pezzi lunghi 30 cm,
2 pezzi lunghi 25 cm
Per un totale di 17 pezzi che in totale fanno 5,20 metri. Ovviamente dalle barre da 2 metri ci saranno degli sfridi inutilizzabili, dunque saranno necessarie almeno 3 o 4 verghe da 2 metri.
Per assemblare la struttura ho usato i raccordi in plastica venduti per le stesse barre di alluminio. Per la precisione ci serviranno:
4 pezzi di giunto a L,
2 pezzi di giunto a T,
4 pezzi di giunto a tre vie,
2 pezzi di giunto a quattro vie,
4 piedini regolabili in plastica
I pezzi vanno montati come si vede nella seguente foto:
.jpg)
Schema di montaggio della struttura tubolare
Vista laterale
Sulla struttura così assemblata ho fissato le guide scanalate per il carrello dell'asse Y (quello che si muove avanti e indietro rispetto all'osservatore. Inizialmente, per questioni di disponibilità ho usato le guide dei cassetti. Anche se apparentemente lo scorrimento sembrava ottimale, in un successivo aggionamento le ho sostituite con delle guide professionali con cursore (slider) a ricircolo di sfere.
Il motivo è che il cursore delle guide per cassetti non è progettato per un utilizzo intensivo, dunque ho avuto problemi di affidabilità.
Stessa cosa per l'asse X, mentre per l'asse Z (quello dell'estrusore) ho mantenuto la vecchie guide per cassetti.
Per l'asse Y ho usato due guide parallele con altrettanti cursori. Il gioco di questi slider è talmente ridotto che non è necessario impiegarne di più. Il movimento è dolce, senza attriti o imperferzioni anche in condizioni gravose o di lunga durata.
Come si vede nelle foto, il motore dell'asse Y è fissato alla barra posteriore della struttura, mentre su quella anteriore è montato un doppio cuscinetto con delle viti che permettono la regolazione. La cinghia passa nella puleggia del motore, prosegue nei cuscinetti e poi sopra la piastra mobile, dove è ancorata con delle viti.
Abbiamo in questo modo ottenuto una slitta mobile in grado di supportare la piastra in alluminio che ospiterà la meccanica dell'asse X.
Su questa piastra ho montato una singola guida con un unico cursore a ricircolo di sfere, sul quale è stabilmente fissata un'altra piastra in alluminio di 210x210 mm. La meccanica del motore, pulegge, cinghie e rinvii è la stessa usata per l'asse Y.
Da notarsi l'intreccio delle cinghie nella parte sottostante.
Sulla piastra in alluminio ho installato l'Heat bed inserendo deli spessori in gomma di 10 millimetri. Nell'intercapedine ho infilato un tappeto quadrato di fibra ceramica (usate nell'isolamento delle caldaie) per ottenere un adeguato isolamento termico. A questo punto possiamo inziare la cablatura dei cavi.
Alla piastra mobile devono arrivare il cavo di alimentazione dell'Heat bed (di sezione 2 mmq) e i due cavetti sottili per il termistore. Consiglio di racchiudere i cavi in una catenaria portacavi flessibile, in modo da evitare che si impiglino durante il movimento (vedi foto).
La catenaria dei cavi è fissata sulla piastra mobile dell'asse X, che prosegue dal lato opposto insieme ad altri cavi: quelli a 4 fili per il motore stepper e due per il microswitch di fine corsa. Tutti questi cavi devono essre portati in prossimità della scheda controller, consiglio di usare delle canalette in plastica.
Ho scelto di installare il controller (Arduino Mega e Ramps 1.4 sulla mensola formata dalla struttura tubolare per questioni di comodità, visto che è comodo avere nei pressi il display LCD e il lettore schede SD integrato.
Dobbiamo ora installare i sensori di finecorsa, che sono dei normalissimi microswitch normalmente aperti.
Quello dell'asse Y va messo sulla parte posteriore della struttura fissa in modo da essere attivato dal movimento del carrello Y.
Quello per l'asse X va montato sul lato destro della piastra mobile in modo da essere attivato dal carrello dell'asse X.
Quello per l'asse Z da messo sotto il carrello dell'asse Z in modo da essere attivato quando l'estremità dell'estrusore va a contatto con il piatto riscaldato. Per maggiori dettagli e soluzioni consigliate studiate le foto nel dettaglio.
Sulla scheda Ramps arrivano perciò: tre serie di quattro cavi per i motori stepper, due serie di due cavi (grossi) per l'Hot end e l'Heat bed), due serie di due fili per i sensori di temperatura, tre serie di due fili per i finecorsa, una serie di due cavi per la ventola asservita, una serie di due fili per l'illuminatore a led (utile per vedere cosa combina la stampante).
Mi raccomando una cablatura pulita ed ordinata, marcando in modo chiaro tutti i cavi, per non impazzire al momento di effettuare i collegamenti. Per avere un'idea precisa di come procedere è utile seguire questo disegno:
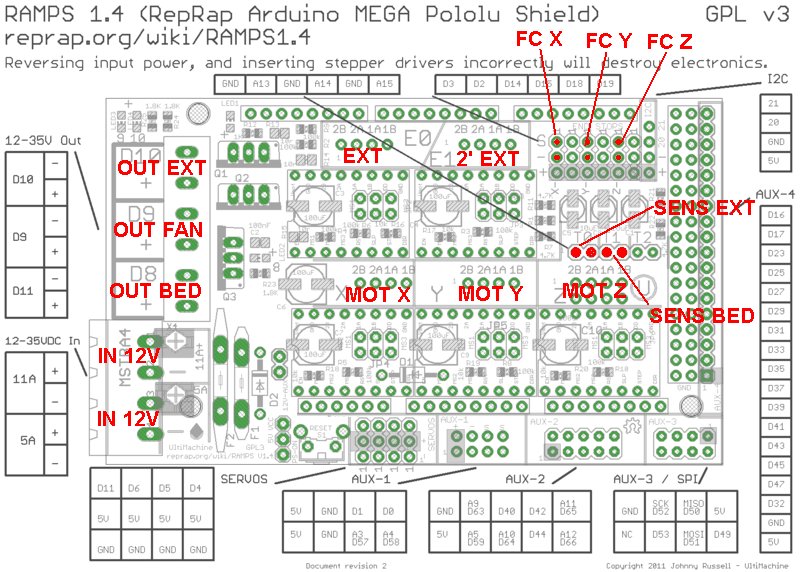
Schema di collegamento alla scheda Ramps 1.4
I collegamenti della scheda Ramp 1.4
Meccanica del carrello mobile dell'estrusore
Il piatto di stampa completo di Heat bed e vetro in borosilicato
Il Firmware
Come firmware, dopo aver provato per alcuni mesi Sprinter, ho scelto Marlin. Si tratta di un progetto Open source sviluppato da una gruppo di appassionati e concesso gratuitamente con licenza GNU GPL v3.
E' scritto in linguaggio Wiring (derivato dal "C") e sviluppato per la piattaforma Arduino, di cui sfrutta l'omonimo compilatore. Il linguaggio macchina è trasferito nella memoria del microprocessore direttamente tramite la porta USB, senza l'ausilio di programmatori esterni.
I parametri che dobbiamo modificare per adattarlo alla nostra architettura si trovano in un'unica sezione, quella denominata "config.h".
Qui possiamo inserire il tipo di scheda usata, gli step dei motori, la direzione dei movimenti, la logica dei finecorsa, gli eventuali add-on (come il display LCD) e molto altro.
La trattazione completa richiederebbe troppo spazio per questo articolo, dunque sarà oggetto di una successivo articolo.
L'ultima versione del firmware da caricare sull'Arduino Mega si trova sul sito di riferimento: http://reprap.org/wiki/Marlin
La prima stampa
Abbiamo terminato la stampante, installato il firmware, controllata la correttezza dei movimenti ed ora dobbiamo collaudarla.
Per prima cosa dobbiamo verificare se i parametri dei motori inseriti nel firmware sono corretti.
Per far questo possiamo stampare un cubo di 20 mm di lato, in modo da misurare al termine della stampa se le dimensioni coincidono.
Per far questo occorre intervenire sul numero di step inserito sul file config.h
Se le dimensioni sono eccessive occorre ridurre il numero dei passi, fino a trovare quelle corrette.
Il numero dipende dai passi/giro dei motori, dall'impostazione dei micropassi, dal diametro delle pulegge ecc. Dunque serve un pò di pazienza.
Esistono anche dei metodi di calcolo per stabilire a priori i parametri, ma al momento non ho trovato indispensabile servirmene.
Vi segnalo anche alcuni brevi video su Youtube, dove si vede la mia stampante in funzione (è ancora una delle prime versioni):
A breve ne seguiranno altri della versione aggiornata.
Nel frattempo auguro un buon lavoro a quelli che vorranno prendere spunto dalla mia Stratos per realizzarne la propria.